In der Lebensmittel- und Getränkeindustrie ist Druckluft – neben Wasser, Elektrizität und Erdgas – der vierte ausschlaggebende Faktor. Die Zuverlässigkeit dieses vierten Faktors hängt vom planbaren Luftdruck ab, weil selbst kleine Lecks kostspielige Schäden anrichten können.
Nachfolgend ein Blick auf die für die Lebensmittel- und Getränkeindustrie typischen Luftlecks sowie auf die bewährten Mittel und Technologien zu deren Bekämpfung.
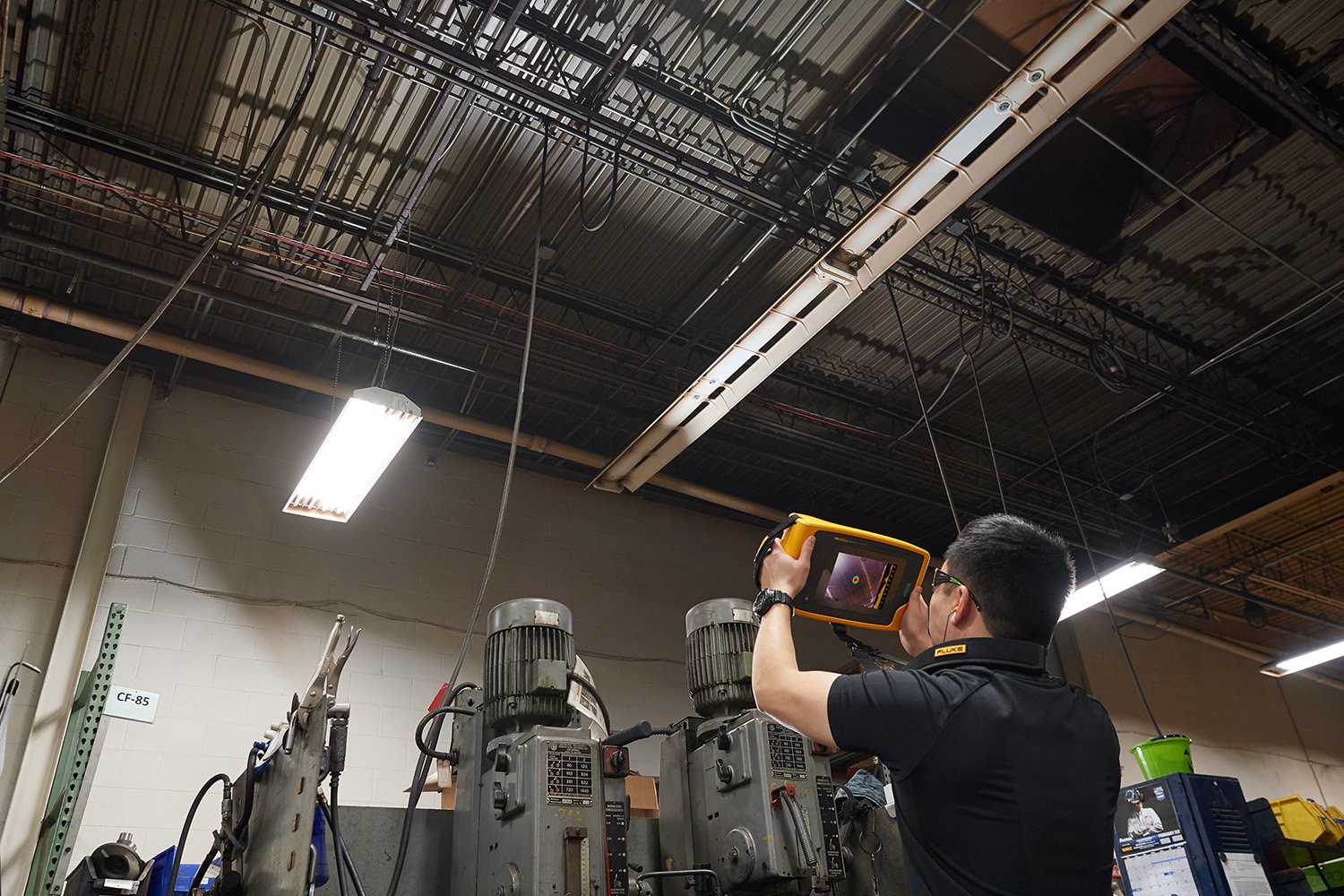
Für Lebensmittel- und Getränkehersteller sind Druckluftlecks ein besonderer Grund zur Besorgnis, da die gleichbleibende Qualität des jeweiligen Produkts ein Schlüsselelement für das Markenimage darstellt, besonders da Produktionsstätten äußerst strengen Kontrollen und Richtlinien zur Kontaminationsvermeidung unterliegen.
In Lebensmittel- und Getränkebetrieben werden mehrere Druckluftanwendungen mittels Leitungen verbunden, um mit der daraus gewonnen Druckluft Produkte zu bewegen, pneumatische Geräte zu bedienen oder Flüssigkeiten, die in der Produktionskette, der Verpackung oder der Reinigung benötigt werden, an die entsprechenden Stellen zu pumpen. Nachfolgend einige Beispiele:
- Snacks und Schutzgasverpackung: Bei der Verpackung von empfindlichen Snacks wird die Umgebungsluft durch ein Gas oder Gasgemisch, häufig Stickstoff oder Kohlendioxid, ersetzt. Die Verwendung von Sauerstoff ist ausgeschlossen, da dieser mit Lebensmittelprodukten, vor allem mit Ölen, chemische Reaktionen verursacht.
- Lebensmittel und Sauberkeit: Druckluft wird gereinigt und gefiltert, um die Lebensmittelsicherheit zu gewährleisten und den richtigen Drucktaupunkt zu erhalten, der zur Verhinderung von mikrobiellem Wachstum erforderlich ist.
- Obst und Gemüse: Bei der Vorbereitung für das Verpacken entfernen Druckluftdüsen effizient Schalen von Obst und Gemüse. Druckluft mit Hochdruck wird auch zum Schneiden von Lebensmitteln als saubere Alternative zu Messern oder Klingen verwendet.
- Brauereien, Gärung und Abfüllung: Druckluft erhöht den Sauerstoffgehalt, um den bakteriellen Fermentationsprozess abzuschließen. Luftverdichter reduzieren den Restsauerstoff während der Abfüllung, und Flaschen werden mit Kohlendioxid gespült und mithilfe pneumatisch angetriebener Maschinen mit Bier befüllt. Brauereien sind warme Arbeitsumgebungen, und ihre Systeme sind daher anfälliger für Lecks.
Jedes Luft- oder Gasleck kann die Produktion verlangsamen, die Produktqualität beeinträchtigen und Sicherheits- oder Kontaminationsprobleme verursachen – und damit hohe Kosten verursachen und Gewinne schmälern.
Die versteckten Kosten des Austritts von Druckluft
Druckluft und Gase müssen mit einem bestimmten Druck zur Verfügung stehen, um die Produktions- und Qualitätsziele zu erreichen. In vielen Anlagen werden Luftlecks jedoch als Betriebskosten hingenommen. Energieverluste können einen großen Teil dieser Kosten ausmachen, aber oft spielen auch andere, weniger leicht erkennbare Faktoren wie Effizienz, Qualität und Ausfallzeiten eine Rolle.
Laut dem vom Compressed Air & Gas Institute (CAGI) herausgegebenen Compressed Air & Gas Handbook Seventh Edition kann „ein einzelnes, circa 6 mm großes Leck in einer Druckluftleitung bereits zu Mehrkosten von 2.500 $ bis über 8.000 $ pro Jahr führen. Das Auffinden und Beheben von Luft- und Gaslecks führt je nach Druckbedarf und Energiekosten zu erheblichen Einsparungen.“
Vorteile der Prüfung von Druckluftsystemen
- Steigerung der Effizienz durch regelmäßige Instandhaltung: Druckluftanlagen, die nach der Installation nicht regelmäßig instand gehalten werden, könnten allein durch Lecks 20 bis 30 Prozent der Druckluft verlieren.
- Kostenreduzierung: Druckabfall wird oft falsch als Geräteausfall diagnostiziert, was zu zusätzlichen Investitionen in neue Luftverdichter führt.
- Weniger Ausfallzeiten: Die durch Druckabfall oder die Installation neuer Anlagen verlorene Produktionszeit zieht Ausfallzeiten nach sich und wirkt sich negativ auf die Produktionsplanung aus. Ungeplante Ausfallzeiten kosten durchschnittlich 200 $ pro Minute und sind daher unbedingt zu vermeiden.
- Verbesserung der Produktqualität: Ein unzureichender Druck führt dazu, dass die Verpackung nicht ordnungsgemäß versiegelt wird oder das Lebensmittelprodukt die einheitlichen Anforderungen an Textur und Geschmack nicht erfüllt.
- Verbesserung der Produktsicherheit: Lecks, die Kontamination verursachen, führen zu hohen Kosten durch Verschwendung, Vertragsstrafen und Schädigung des guten Rufs.
- Reduzierung der CO₂-Bilanz: Systeme mit Luft- und Gaslecks werden ineffizient, was sich auf die CO₂-Bilanz eines Unternehmens auswirkt und verhindert, dass Nachhaltigkeits- oder Umweltziele erreicht werden.
Die Formel zur Bestimmung des Ausmaßes von Druckluftlecks in einer Anlage lautet: Leck (%) = (T x 100) ÷ (T + t)T = Aufladezeit (Minuten), t = Entladezeit (Minuten)
Wenn das Druckluftsystem mit Start-/Stopp-Steuerungen konfiguriert ist, muss der Druckluftverdichter gestartet werden, wenn kein Systembedarf besteht – nach Betriebsende oder außerhalb der Schicht. Dann sollte mehrfach das An- und Abschalten der Verdichter und dabei Messungen durchgeführt werden, um die durchschnittliche Zeit zur Druckluftentladung des Systems zu bestimmen.
Verfahren zur Erkennung und Behebung von Luftlecks
Der erste Schritt bei der Kontrolle der Prozesse und Kosten ist das Auffinden des Ursprungs der Lecks. Hier eine Liste der häufigsten Leckstellen:
- Kondensatabscheider
- Verschraubungen
- Armaturen
- Flansche
- Kombinationen aus Filtern, Reglern, Schmiervorrichtungen
- Schläuche
- Dichtungen
- Pneumatische Vorratsbehälter
- Schnellkupplungen
- Rohrverbindungen mit Gewinden
- Rohrleitungen
- Ventile
Luft- und Gaslecks sind ein großes Problem, weil sie häufig vorkommen und schwer zu finden sind. Sobald sie gefunden und behoben wurden, besteht die Wahrscheinlichkeit, dass aufgrund der normalen Abnutzung des Systems weitere Lecks auftreten.
Auch wenn es eventuell nicht möglich ist, jedes einzelne Leck zu beseitigen, so kann doch die Gesamtzahl durch gezielte Inspektion mithilfe herkömmlicher Erkennungsmethoden reduziert werden. Bei diesen Methoden wird ein Leck mit einem Papieretikett markiert, sobald es gefunden wurde. Zu den vier herkömmlichen Erkennungsmethoden gehören:
- Tonsignale: Zischen weist auf Lecks hin und bedeutet, dass das Leck beträchtlich ist, da nur ein Schallpegel von über 60 dBA ohne Erkennungsgeräte für Lecks zu hören ist. Da die meisten Anlagen hohe Betriebslautstärken aufweisen und häufig Gehörschutz benötigt wird, muss während der Stillstandzeiten – zwischen Schichten, am Wochenende oder während der planmäßigen Instandhaltung – auf Lecks geprüft werden.
- Wasser und Seife: Techniker sprühen Seifenwasser auf Bereiche mit hörbaren Lecks. An Stellen, an denen Blasen auftreten, befindet sich ein Leck. Diese Methode ist langwierig, alles andere als präzise und erfordert eine nachgelagerte Reinigung, da das Seifenwasser eine Rutschgefahr darstellt. Bei einigen sauberen und kontaminationsgeschützten Prozessen ist sie nicht zulässig.
- Akustische Ultraschallerkennung: Während der Stillstandzeit scannen Techniker, die Ohrhörer tragen, mögliche Leckstellen mit einem Parabolsensor oder einem konischen Sensor. Wenn ein Geräusch erkannt wird, das auf ein Leck hinweist, kommt ein stabförmiger Sensor zur Anwendung, der zur genauen Positionsbestimmung einige Zentimeter vom Leck entfernt gehalten werden muss.
- Einsatz externer Experten: Ingenieure oder andere Experten werden in der Regel einmal pro Jahr beauftragt, um Kosten einzusparen und Unterbrechungen zu verhindern. Sie verwenden eine oder alle traditionellen Techniken, Reparaturen und Kontrollen.
Keine dieser Methoden ist fehlerfrei und die meisten führen zu Ausfallzeiten, was sowohl Zeit als auch Geld kostet.
Mit der Prüfung auf Druckluftlecks erzielt eine Kaffeerösterei Energieeinsparungen von 10 %
Projektingenieure einer Kaffeerösterei nahmen in einer Anlage mit erhöhter Wahrscheinlichkeit von Druckluftlecks an einer Pilotstudie zur Schallbildgebung zur Erkennung von Lecks teil. Die Prüfungen ergaben, dass das Unternehmen durch den Einsatz eines neuen Geräts zur Leckerkennung mehr als 10 % seines jährlichen Energieverbrauchs einsparen könnte.
Die 300.000 Quadratmeter große Anlage verfügt über einen Röst- und Verpackungsbereich für Kaffee, einen Nassprozessbereich für Kaffee sowie einen Bereich für das Mischen und Verpacken von Tee. Alle diese Vorgänge erfordern einen korrekten Luftdruck, um Prozesse effizient abzuschließen, und herkömmliche Methoden der Leckerkennung waren nicht mehr ausreichend.
An einem durchschnittlichen Tag verbraucht das Werk zwischen 28 und 45 Kubikmeter Druckluft pro Minute. Das Druckluftsystem des Unternehmens, das aus fünf Luftverdichtern mit einer Gesamtleistung von 430 kW besteht, versorgt die Automatisierung und die Rohre und Schläuche, die zur Versorgung des Stickstofferzeugungssystems des Betriebs verwendet werden. Stickstoff wird verwendet, um die Qualität des Kaffees zu verbessern. Darüber hinaus wird das Schutzgas für das Mischen von Tee verwendet.
Mit der Schallkamera Fluke ii900 ermittelte das Team potenzielle Energieeinsparungen von 10 %, was auch dem Nachhaltigkeitsziel des Unternehmens entspricht. Der neue Ansatz zeigte zudem, wie das Team den Prozess der Erkennung von Luft- und Gaslecks vereinfachen konnte, sodass die Mitarbeiter auch ohne Zeitaufwand für das Erkennen und Beheben von Lecks weiterarbeiten können.
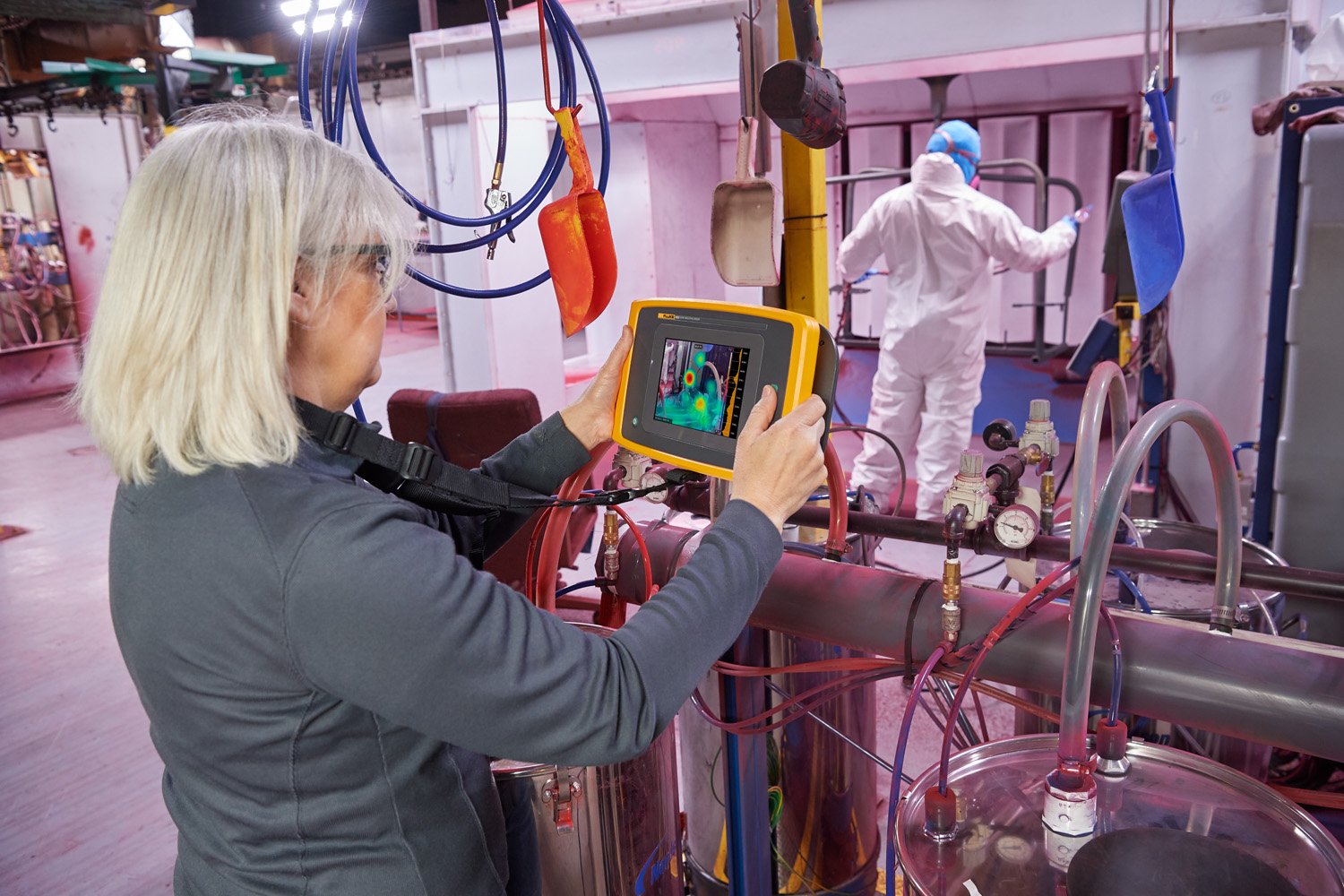
Mit einer Schallkamera zum ersten Mal Luftlecks sehen
Die innovative Technologie zur Leckerkennung mittels einer tragbaren industriellen Schallkamera erleichtert die Erkennung von Lecks und die Vermeidung damit einhergehender Verluste.
Die Schallkamera Fluke ii900 ermöglicht es Anwendern, Luftlecks auf einem LC-Bildschirm in Echtzeit zu lokalisieren und zu sehen. Die einfache Bedienung mit Anvisieren und Aufnehmen des Schallbilds kann auch von nicht spezialisierten Technikern genutzt werden. Die meisten Anwender benötigen etwa 10 Minuten, bis sie mit dem Verfahren vertraut sind. Darüber hinaus ermöglicht es Technikern, bei laufenden Geräten aus sicherer Entfernung zu arbeiten. Außerdem erleichtert das Gerät das Erkennen von Lecks in schwer zugänglichen Bereichen sowie die Unterscheidung mehrerer, nah beieinander liegender Lecks.
Das handliche Bildgebungsinstrument verfügt über eine Anordnung von mehreren hochempfindlichen Mikrofonen, die Geräusche im hörbaren Bereich sowie im Ultraschallbereich erkennen und diese visuell abbilden. Das Gerät wendet dann proprietäre Algorithmen auf die Ergebnisse an und erstellt sofort eine visuelle Karte des Lecks auf dem Bildschirm. Das Bild des Lecks wird über dem Sichtbild des Bereichs überlagert, sodass der Bediener die Leckstelle schnell lokalisieren kann.
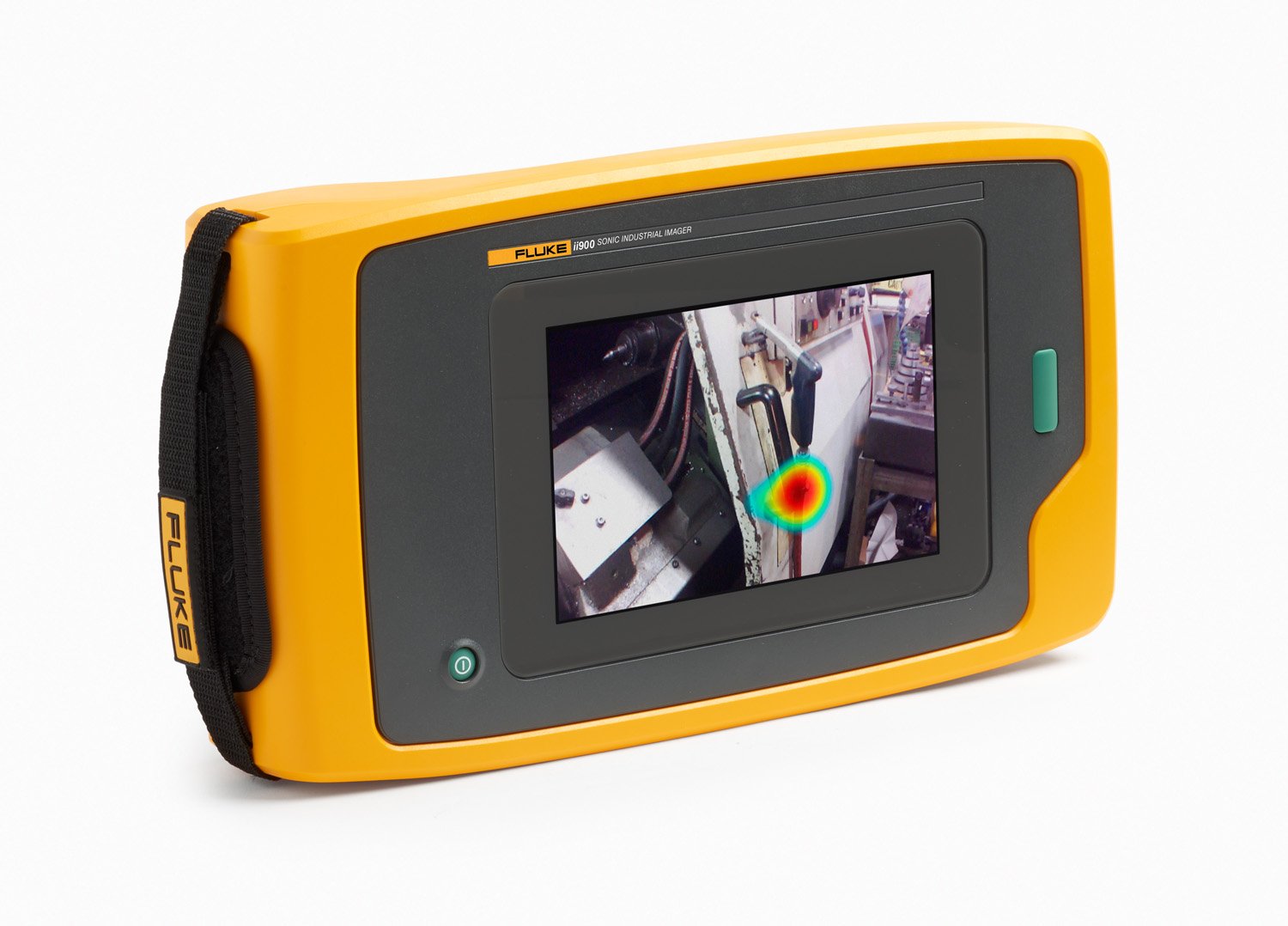
Die Fluke ii900 kann auch verwendet werden, um Reparaturen zu überprüfen. Zudem können Aufnahmen, die als Standbilder oder Live-Videos aufgenommen wurden, geteilt und mit Kollegen diskutiert werden, falls Unklarheiten oder Fragen aufkommen. Durch die erfassten Bilder wird es überflüssig, Leitern zu erklimmen oder Lecks mit den üblichen empfindlichen Etiketten zu markieren.
So zahlen Sie weniger für verborgene Luftlecks
Mittels der herkömmlichen und neuen Erkennungsverfahren sollten durch Luft- und Gaslecks entstehende versteckte Kosten und Verschwendung jetzt verhindert werden. Zu den bewährten Verfahren gehören:
- Der Systemansatz: Häufig erhöht die Behebung eines Lecks den Systemdruck, wodurch kleinere Lecks größer werden und das gesamte System beeinträchtigt wird. Änderungen lassen sich mit Gesamtstrategien für einen verbesserten Energieverbrauch und robustere Steuerungssysteme kombinieren. Dies ist eine große Herausforderung, jedoch ergeben Investitionen an den richtigen Stellen häufig Energieeinsparungen und amortisieren sich dadurch schnell.
- Häufige Prüfungen: Häufiges Prüfen – d. h. häufiger als die üblichen jährlichen oder vierteljährlichen Leckprüfungen – spart langfristig Zeit, Geld und Ressourcen, selbst wenn Anlagen abgeschaltet werden müssen. Mit neuer Bildgebungstechnologie können Lecks beseitigt und kontinuierlich behoben werden, ohne wertvolle Produktionszeit zu verlieren.
- Ursachen für Druckabfälle feststellen: Druckabfall kann fälschlicherweise als Geräteausfall diagnostiziert werden. Bevor Investitionsausgaben getätigt werden, können Leckprüfungen und Fehlerbehebungen Tausende oder sogar Hunderttausende von Dollar einsparen und den benötigten Druck sofort wiederherstellen.
- Protokollieren, verfolgen und überprüfen im Zeitverlauf: Es ist wichtig, genau zu erfassen, wo Lecks aufgetreten sind, da an diesen Schwachstellen in der Regel am ehesten neue Lecks auftreten. Diese Bereiche sind regelmäßig zu inspizieren. Die Online-Protokollierung von Informationen ermöglicht die einfache Weitergabe und Verwendung von Daten, um so den Prüfprozess nachhaltig und konsistent zu gestalten. Prüfungen sollten außerdem kurz nach Reparaturen erfolgen, um festzustellen, ob Lecks beseitigt wurden oder weitere Aufmerksamkeit erfordern.