Angesichts des wirtschaftlichen Abschwungs müssen viele Betriebsleiter mit sehr knappen Budgets für Betrieb und Wartung auskommen. Die Kapitalausgaben für neue mechanische HLK-Geräte wurden wahrscheinlich entweder eingefroren oder gestrichen.
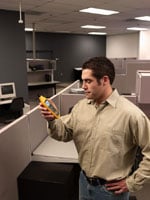
Eine Möglichkeit, den finanziellen Spielraum zu erweitern, besteht darin, die vorhandenen HLK-Geräte besser einzustellen. Wenn Sie sich an die bewährten Wartungsverfahren halten, wird die höhere Betriebseffizienz zu einer Verringerung des Energieverbrauchs führen. Kumulative Einsparungen bei den Stromkosten können das allgemeine Budget ergänzen.
Während HLK-Systeme hinsichtlich der Geräte und Betriebseigenschaften stark variieren, sollte die folgende Checkliste für die meisten Hauptgerätetypen und Energieverschwendungsbereiche gelten:
Dampfsystem-Checkliste:
Isolationsprüfungen:
Lose oder fehlende Isolation kann Tausende von Euro zusätzliche Heizkosten pro Heizsaison kosten. Verwenden Sie eine Wärmebildkamera zur Inspektion der Systemisolierung und zum Erkennen mangelhafter Bereiche.
Kondensatabscheider-Prüfungen:
Kondensatabscheider scheiden Kondenswasser von Heiz- und Prozessmaschinen ab. Bei fehlerhafter geöffneter Stellung der Abscheider geht wertvoller Dampf verloren. Um einen fehlerhaften Abscheider erkennen zu können, vergleichen Sie mithilfe einer kontaktlosen Wärmebildkamera, eines Infrarot-Thermometers oder eines Kontaktthermometers die Temperatur des Abscheiders mit der Rohrtemperatur auf einer der beiden Seiten. Thermografie- und Infrarot-Thermometer bieten offensichtliche Vorteile bei Abscheidern, die in schlecht zugänglichen Bereichen montiert sind. Normale Temperaturunterschiede zwischen Kondensatabscheidern liegen bei ungefähr 11 °C.
Prüfen Sie die Lufttemperaturen im Heizkesselraum:
Für eine ordnungsgemäße Verbrennung muss die Temperatur der Verbrennungsluft im gültigen Bereich liegen. Verwenden Sie ein Digitalthermometer, das zur Messung von Umgebungslufttemperaturen konzipiert ist, und prüfen Sie gegebenenfalls auch das Kohlenmonoxidniveau im Heizkesselraum, um die Sicherheit zu gewährleisten.
Andere:
Zusätzlich zu den oben vorgenommenen Schritten prüfen Sie auch die Speisewassertemperatur, die Kraftstoffölheizungstemperatur und andere Punkte wie das Schmiermittel. Diese Prüfungen können nicht nur Energie, sondern auch Kosten für die Reparatur und den Ausfall von Geräten sparen.
Kühlsystem-Checkliste:
Elektrische Prüfungen:
Prüfen Sie Spannung und Stromstärke des Kompressors, um sicherzustellen, dass der Motor auf den vom Hersteller empfohlenen Niveaus fährt.
Temperaturprüfungen:
Prüfen Sie, ob die Temperaturen von Ein- und Auslassluft und die Wassertemperaturen an den Wärmetauschern auf maximale Effizienz eingestellt sind. Die Kühlwasserzufuhrtemperaturen für Wassersysteme sollten zwischen 5,6 und 6,7 °C liegen.
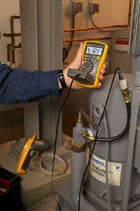
Druckprüfungen:
Verwenden Sie ein Digitalmultimeter mit einem Druckanschluss zur Messung der Ein- und Auslassdrücke von Schale und Rohrwärmetauschern, um sicherzustellen, dass die Rohre nicht verunreinigt sind. Eine Verunreinigung führt zu einer geringeren Wärmeübertragung und einem höherem Energieverbrauch am Kompressor. Der Druckabfall am Wärmetauscher (Delta P) kann zwischen 345 und 724 mbar liegen und hängt vom Hersteller ab.Prüfen Sie das Kältemittel und auch die Pumpendrücke, um sicherzustellen, dass die Maschine auf Basisniveau läuft.
Kühlturmprüfungen:
Damit Kühlgeräte möglichst effizient betrieben werden können, muss der Kühlturm ordnungsgemäß arbeiten. Da Kühltürme die Wärme mit einer bestimmten Geschwindigkeit in die Atmosphäre abgeben, verwenden Sie ein Temperatur-/Feuchtigkeitsmessgerät zur Messung der Außenlufttemperatur und -feuchte und analysieren den Betrieb des Kühlturms. Messen Sie außerdem die Temperatur des dem Kühler zugeführten Kondenswassers. Ein häufiger Wert ist 29 °C.
Lüftungssystem-Checkliste:
Elektrische Prüfungen:
Messen Sie Spannung und Stromstärke des Lüftermotors und vergleichen Sie diese mit den Angaben auf dem Typenschild.
Temperaturprüfungen:
Prüfen Sie die folgenden Werte in den Luftaufbereitungen:
- Außenlufttemperatur
- Mischlufttemperatur
- Rücklufttemperatur
- Abluft- oder Versorgungslufttemperatur
- Ablufttemperaturen an der Spulenoberfläche
- Raumtemperatursensoren
- Economizer und zugehörige Klappen
- Sensoren für Feuchtkugeltemperatur oder relative Feuchte
Erfassen Sie die Messwerte mit einem Handtemperaturmessgerät und vergleichen Sie sie mit den Werten des Steuersystems, um die Genauigkeit zu gewährleisten. Die Sensorkalibrierung sollte fester Bestandteil sämtlicher Wartungsprogramme sein.
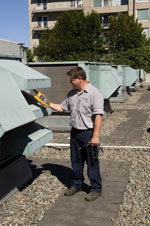
Luftdruckprüfungen:
Prüfen Sie die Druckabfälle in den Filterbänken, um einen ungehinderten Luftstrom zu gewährleisten. Übermäßige Druckabfälle führen zu einem höheren Energieverbrauch. Messen Sie die Luftdruckabfälle in Heizregistern und Kühlschlangen, um sich von ihrer Sauberkeit zu überzeugen. Messen Sie die Ein- und Auslasslufttemperaturen, um die Temperaturanstiege und -abfälle zu optimieren.
Beleuchtungssystem-Checkliste:
Elektrikprüfungen: Zu den Thermografieanwendungen für die Beleuchtung gehören die Kontakttemperaturen von Vorschaltgerät und Unterbrecher. Suchen Sie nach heißen Stellen und vergleichen Sie die Werte zur Analyse mit den Ausgangswerten oder vorherigen Temperaturmessungen. Verwenden Sie einen Belichtungsmesser zur Messung von Beleuchtungsstärke (Lux) oder Lichtstrom (Lumen). Reduzieren Sie nach Möglichkeit die Beleuchtungsstärke auf die Industriestandards. Erwägen Sie insbesondere eine Reduzierung der Beleuchtung in Jahreszeiten, in denen mehr natürliches Licht vorhanden ist. Speichern Sie in einem Messgerät mit Aufzeichnungsfunktion die Beleuchtung eines Betriebs außerhalb der Arbeitszeit. Dadurch können Sie Bereiche identifizieren, in denen das Licht versehentlich oder unnötigerweise eingeschaltet bleibt. Verwenden Sie ein Netzqualitätsmessgerät zur Analyse von Spannung, Stromstärke und Energieverbrauch in kWh in Ihrem Betrieb. Protokollieren Sie nach Möglichkeit den Energieverbrauch über die Zeit in bestimmten Stromkreisen und von bestimmten Geräten und Bereichen. Vergleichen Sie Ihren stündlichen Verbrauch mit Ihrer Gebührenstruktur und steuern Sie Ihr Verbrauchsverhalten so, dass sie Zeiten mit hoher Nachfrage und hohen Kosten meiden. Prüfen Sie außerdem die Versorgungsspannungen des Steuersystems, um den einwandfreien Betrieb der Steuerung sicherzustellen. Die Kommunikationsbuswerte der Steuerung können geprüft werden, um die Integrität der Kommunikationsverkabelung zu gewährleisten. Prüfen Sie alle Sensoren und Thermometer auf ordnungsgemäß kalibrierte Messgeräte. Prüfen Sie auch Ventil- und Klappenaktoren. Aktorenprobleme können zu einem vermehrten Gebrauch von Heizung und Kühlung und höheren Stromrechnungen führen. Die Ausgangsspannungen und Stromsignale der Aktoren können mit einem normalen Digitalmultimeter geprüft werden. Prüfen Sie, ob die Temperaturen von Ein- und Auslassluft und die Wassertemperaturen an den Wärmetauschern auf maximale Effizienz eingestellt sind. Die Kühlwasserzufuhrtemperaturen für die meisten Kühlwassersysteme liegen beispielsweise zwischen 5,6 und 6,7 °C. Protokollieren Sie die Lufttemperatur über die Zeit, über besetzte und unbesetzte Pläne, identifizieren Sie Bereiche, die über Nacht oder an Wochenenden im falschen Temperaturmodus belassen werden und dadurch Energie verschwenden. Prüfen Sie die Genauigkeit aller Sollwerte für Temperatur, Druck und Feuchte, indem Sie diese Werte über die Zeit protokollieren. Durch eine ungenaue Steuerung kann es zu einer Verschwendung von 1 % Energie pro Grad Abweichung kommen.Beleuchtungsniveaus:
Betriebsprüfungen:
Checkliste für den Aufbau eines Automationssystems:
Energieverbrauchsprüfungen:
Steuerungssystem:
Temperaturprüfungen:
Betriebsprüfungen:
Sollwertprüfungen: