Was haben Messungen mit Energiesparen zu tun? Es geht immer um die Rendite und das Geschäftsergebnis.
Industrieanlagen benötigen Energie, um Produkte oder auch Daten zu verarbeiten, und die meisten Anlagen verbrauchen mehr Energie als nötig. Sie sind ineffiziente Energieverbraucher. Vor zwanzig Jahren war Energieeffizienz ein nachrangiges Thema für die Werksleitung – Energie war noch preisgünstig. Je teurer die Energie wurde, desto mehr interessierten sich die Werksleiter für eine Senkung der Energiekosten. Dabei mussten die Maßnahmen aber auch wirtschaftlich durchführbar sein.
Doch wo ist der Punkt, wo sich Investitionen in die Verringerung der Energieverluste lohnen, um die Rendite nicht zu gefährden?
Um diese Frage zu beantworten, müssen Sie messen, wie viel Energie Sie für die verschiedenen Systeme und Arten von Arbeit in Ihrem Gebäude verbrauchen, und mit den relevanten Normen vergleichen. Daraus können Sie dann ersehen, wie viel Energie verschwendet wird. Weitere Messungen können beim Ermitteln der Ursachen hilfreich sein. Die drei Punkte einer Rentabilitätsgleichung sind: 1) die Menge der Verschwendung kombiniert mit 2) der Ursache und 3) den zu betrachtenden Kosten.
Wann ist eine Reduzierung des Energieverbrauchs sinnvoll?
Eine Reduzierung des Energieverbrauchs ist sinnvoll für Betriebe, die ihre Gemeinkosten senken möchten, um die Produktivität zu erhöhen – Betriebe, die mit geringeren Mitteln mehr erreichen und nicht nur weniger ausgeben möchten.
Eine Energieprüfung zeigt Möglichkeiten zur Effizienzsteigerung auf und liefert dem Betriebsleiter die notwendigen Daten, um zu verstehen, welche Aktivitäten zur Energieeinsparung unter Berücksichtigung der Primärziele des Betriebs sinnvoll sind und welche entweder nicht genug Rendite bieten oder zu weit an den Prioritäten vorbeigehen. Die größten Möglichkeiten bieten sich meist in Betrieben, die über alte, große Systeme mit hohem Energieverbrauch verfügen, die noch nicht optimiert wurden. Weitere aussichtsreiche Kandidaten sind Fertigungsbetriebe, die noch nicht viele Automatisierungs- oder Steuerungssysteme eingeführt haben, sowie Betriebe mit großen Dampf- oder Druckluftsystemen.
Wie hoch ist das Einsparpotenzial?
Laut Angaben des Energieministeriums der USA könnten Produktionsstätten ihre Energiekosten um 25 % senken, wobei aber die tatsächlichen Einsparungen von mehreren Faktoren abhängig sind. Erstens: Welche Art von Systemen und Aktivitäten gibt es im Betrieb? Große Lasten, die nie mit dem Tarifmodell des Energieversorgers abgestimmt wurden, um die günstigsten Tageszeiten zu nutzen, haben das Potenzial für deutliche Einsparungen. Ein Betrieb, in dem vor allem kleinere Lasten gefahren werden, hat möglicherweise weniger Potenzial. Zweitens: Wie ineffizient sind die Gebäudesysteme? Neuere, regelmäßig instand gehaltene Anlagen bieten nicht so viele Einsparmöglichkeiten wie ältere, in denen die Systeme und Geräte im Laufe der Zeit von den empfohlenen Einstellungen und Instandhaltungsverfahren abgewichen sind.
Wenn man an Energieverschwendung zu Hause denkt, kommt man wohl auf kalte Luft, die durchs Fenster eintritt, oder an alte Glühbirnen, die man durch LEDs ersetzen könnte. Aber welche Art der „Energieverschwendung“ geschieht in einem Fertigungsbetrieb oder einem Mischbetrieb?
Wenn Sie Energie zum Erwärmen oder Kühlen von Luft verbrauchen und dabei die Luft durch das Lüftungssystem zu leiten, nur um sie dann durch das Fenster entweichen zu lassen, zwingen Sie das System zu einer Überproduktion. Wie viele andere Systeme in dem Betrieb arbeiten aufgrund von verstopften Filtern, überdimensionierten Motoren und aus anderen Gründen mit mehr Energieeinsatz als sie sollten?
In einem Fertigungs- oder Mischbetrieb kann es auch zu Energieverschwendung durch Beleuchtung und Gebäudehülle kommen. Aber sind das auch die ersten Punkte, auf die man achten sollte?
Diese Frage können Sie erst beantworten, wenn Sie die Leistungsaufnahme an allen großen Lasten protokollieren, sie mit Tarifmodell und Betriebsplanung abgleichen und die Renditeberechnung durchführen. Ziemlich häufig werden in einem Betrieb genügend Einsparungsmöglichkeiten bei Instandhaltung und Betrieb großer Geräte entdeckt, mit denen innerhalb weniger Jahre genügend Geld eingespart werden kann, um das Ersetzen der Geräte durch kleinere Geräte zu beschleunigen.
Wie Sie bei begrenztem Budget, begrenzter Zeit und begrenzten Ressourcen mit einer Reduzierung des Energieverbrauchs beginnen
Fangen Sie bei den grundlegenden Energiedaten an.
Ermitteln Sie zuerst, wo, wann und wodurch Energie verbraucht wird. Wenn Eigentümer, Manager und Techniker eines Betriebs genau verstehen, wie viel Energie für den Betrieb des Unternehmens benötigt und wie viel Energie verschwendet wird, können sie Entscheidungen treffen und einen Plan erstellen. Um dies zu erreichen, sollten Sie sich zunächst die letzten Stromrechnungen besorgen und nach Anzeichen für Strafzahlungen und Lasten mit Spitzenbedarf suchen. Laden Sie eine Kopie des Tarifmodells von der Website des EVU herunter, damit Sie im Abgleich mit Ihrer Betriebsplanung erkennen können, wie viel die Energie für Ihre Geräte zu verschiedenen Tageszeiten kostet. Rufen Sie bei Bedarf direkt den Kundenservice des EVU an, wo man Ihnen gerne weiterhelfen wird.
Beauftragen Sie dann Ihr eigenes Team oder einen Elektroinstallateur, die Energie an den Eingängen der Versorgungsleitungen sowie an den Spannungsversorgungen der größten Systeme und Lasten zu protokollieren. Zeichnen Sie Wirkleistung, Scheinleistung und Leistungsfaktor über einen repräsentativen Zeitraum auf. Auf diese Weise erhalten Sie ein sehr genaues Bild Ihres tatsächlichen Energieverbrauchs in dreiphasigen Stromkreisen und Lasten. Die größten Einsparungen ergeben sich häufig durch eine Verlagerung des Betriebs von Lasten auf Tageszeiten mit günstigeren Energiekosten.
Welche Systeme sind die größten Energieverschwender?
Nehmen Sie neben der Betrachtung des elektrischen Versorgungssystems auch eine Bewertung Ihre elektromechanischen, Dampf- und Druckluftsysteme vor. Hier wird üblicherweise viel Energie vergeudet, was sich aber auch recht einfach beheben lässt.
Elektromechanik
Es gibt fünf gängige Arten von Energieverschwendung in einem elektromechanischen System: 1) elektrisch, 2) mechanisch/Reibung, 3) Planung, 4) Steuerung und 5) Dimensionierung/Effizienz.
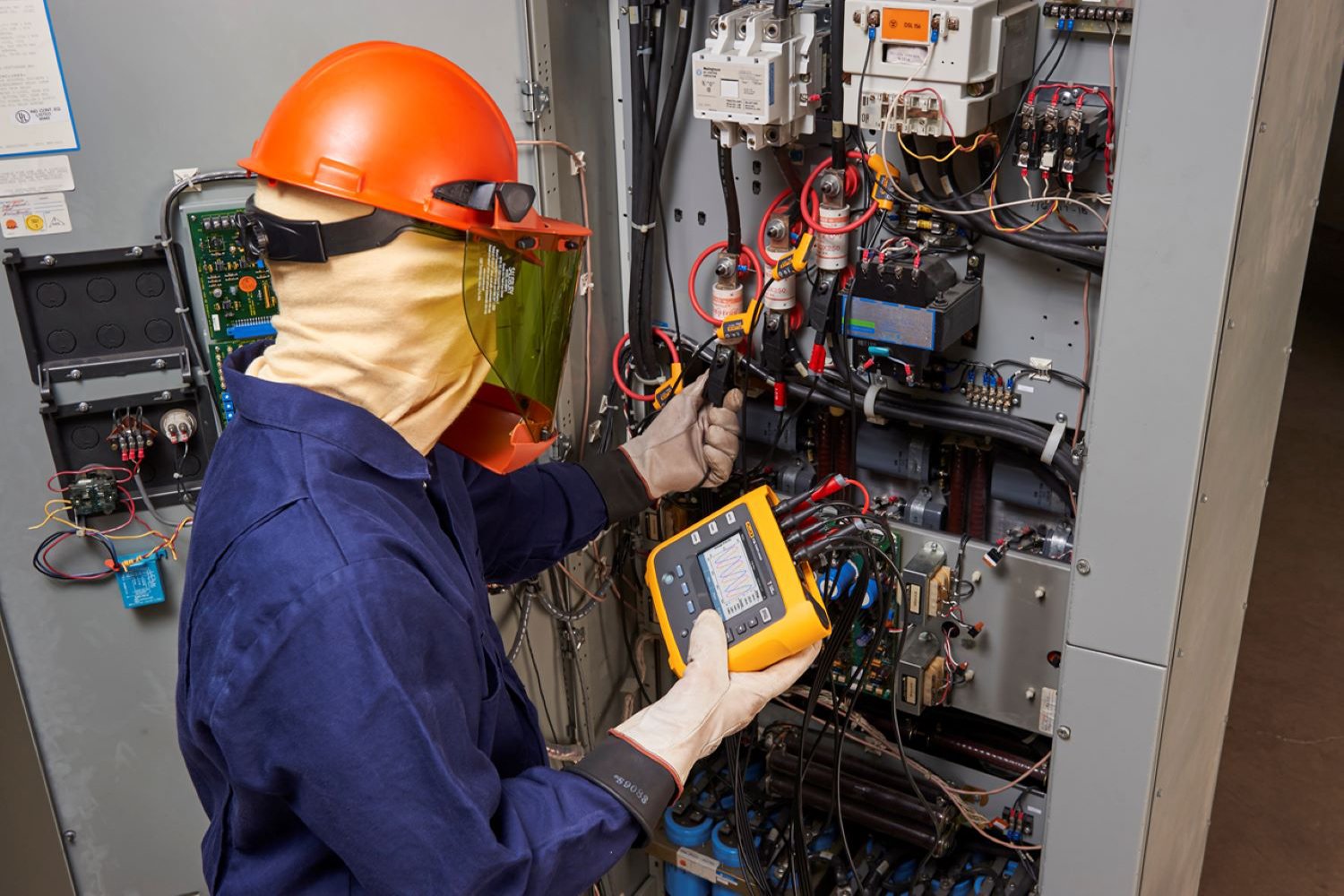
Einsatz eines dreiphasigen Netzqualitäts-Loggers Fluke 1738 für Energiestudien an einem mechanischen System
- Spannungs-/Stromüberlast und Unsymmetrie der Phasen sind zwei wesentliche Ursachen von Energieverschwendung in elektromechanischen Systemen. Beide genannten elektrischen Probleme lassen sich mit Netzqualitäts-Loggern und -Analysatoren und Wärmebildkameras erkennen.
- Mechanische Betriebszustände, bei denen Energie verschwendet wird, zeigen sich als Überhitzung und übermäßige Schwingungen, die durch Wärmebildkameras und Schwingungsmessgeräte erkennbar sind. Mögliche Ursachen variieren von Kühlung und Luftströmung bis hin zu Lagerausrichtung und anderen Ursachen für Reibung. Untersuchen Sie mit einer Wärmebildkamera Kupplungen, Wellen, Riemen, Lager, Lüfter, elektrische Komponenten, Verteiler/Anschlusskästen und Wicklungen – hier können ineffizienter Betrieb und damit Energieverschwendung auftreten.
- Wie bereits beschrieben, ist eine der einfachsten Energiesparlösungen die Protokollierung der Leistungsaufnahme großer elektromechanischer Lasten während des Betriebs. Ermitteln Sie, wann die Maschine die meiste Energie verbraucht (häufig beim Start), und prüfen Sie, ob die Betriebszeiten auf Tageszeiten gelegt werden können, zu denen die Stromtarife am günstigsten sind.
- Prüfen Sie anhand desselben Energieprotokolls die Betriebsplanung darauf hin, wie oft die Maschine Energie verbraucht. Wie viel Energie wird verbraucht, wenn die Maschine nicht aktiv genutzt wird? Ohne Nutzung von Steuerungen müssen die meisten Maschinen manuell ausgeschaltet werden, damit sie keine Energie mehr verbrauchen. Manuelle Aktionen werden jedoch nicht immer ausgeführt. Nicht alle Maschinen können realistischerweise abgeschaltet werden, aber die meisten können in einen Energiesparmodus versetzt werden. Steuerungen variieren von einfach bis vollautomatisch. Es können Sensoren und Zeitschaltungen eingesetzt werden, um Maschinen in den Energiesparmodus zu versetzen, oder auch Änderungen durch eine SPS ausgeführt werden.
- Die Anpassung der Leistung und des Wirkungsgrads von Motoren ermöglicht hohe Einsparungen. Besonders in älteren Betrieben ändern sich die betrieblichen Anforderungen, aber die Lasten bleiben wie sie sind. Das bedeutet, dass manchmal ein großer, teurer und schwer zu startender Motor für den Antrieb eines Systems mit einer geringeren Leistungsaufnahme eingesetzt wird. Jeder Betriebsleiter versucht natürlicherweise, die Lebensdauer einer großen Maschine zu maximieren. Es lohnt sich jedoch zu protokollieren, wie viel Leistung der Motor verglichen mit den tatsächlichen Lastanforderungen und mit einer neuen, hocheffizienten und richtig bemessenen Maschine aufnimmt. Berechnen Sie, wie viel Energie unnötig verbraucht wird, und multiplizieren Sie diesen Wert mit dem entsprechenden Wert des Tarifs des EVU. Ermitteln Sie, wie lange ein neuer Motor brauchen würde, um sich zu rentieren: Manchmal macht es finanziell Sinn, Maschinen zu ersetzen, bevor sie ausfallen. Überlegen Sie andererseits, ob Steuerungen zur Anpassung der Ausgangsleistung verwendet werden können.
Dampf
Die Prozessheizung ist für einen beträchtlichen Anteil der steuerbaren Betriebskosten verantwortlich. Das System muss regelmäßig inspiziert werden, um Betriebszustände zu vermeiden, bei denen Energieverschwendung auftritt.
Protokollieren Sie zunächst den Energieverbrauch am Heizkessel, um sich einen ersten Eindruck über den Energieverbrauch zu verschaffen. Inspizieren Sie anschließend das Verteilungssystem mit Kondensatabscheidern, Manometern, Dämmungen, Pumpen und Ventilen. Identifizieren Sie mit einer Wärmebildkamera ausgefallene Kondensatabscheider, Lecks, Blockierungen, Qualitätsprobleme und Kondensatausfall: Das Ziel besteht darin, möglichst viel vorgewärmtes Kondensat in den Heizkessel zurückzuleiten.
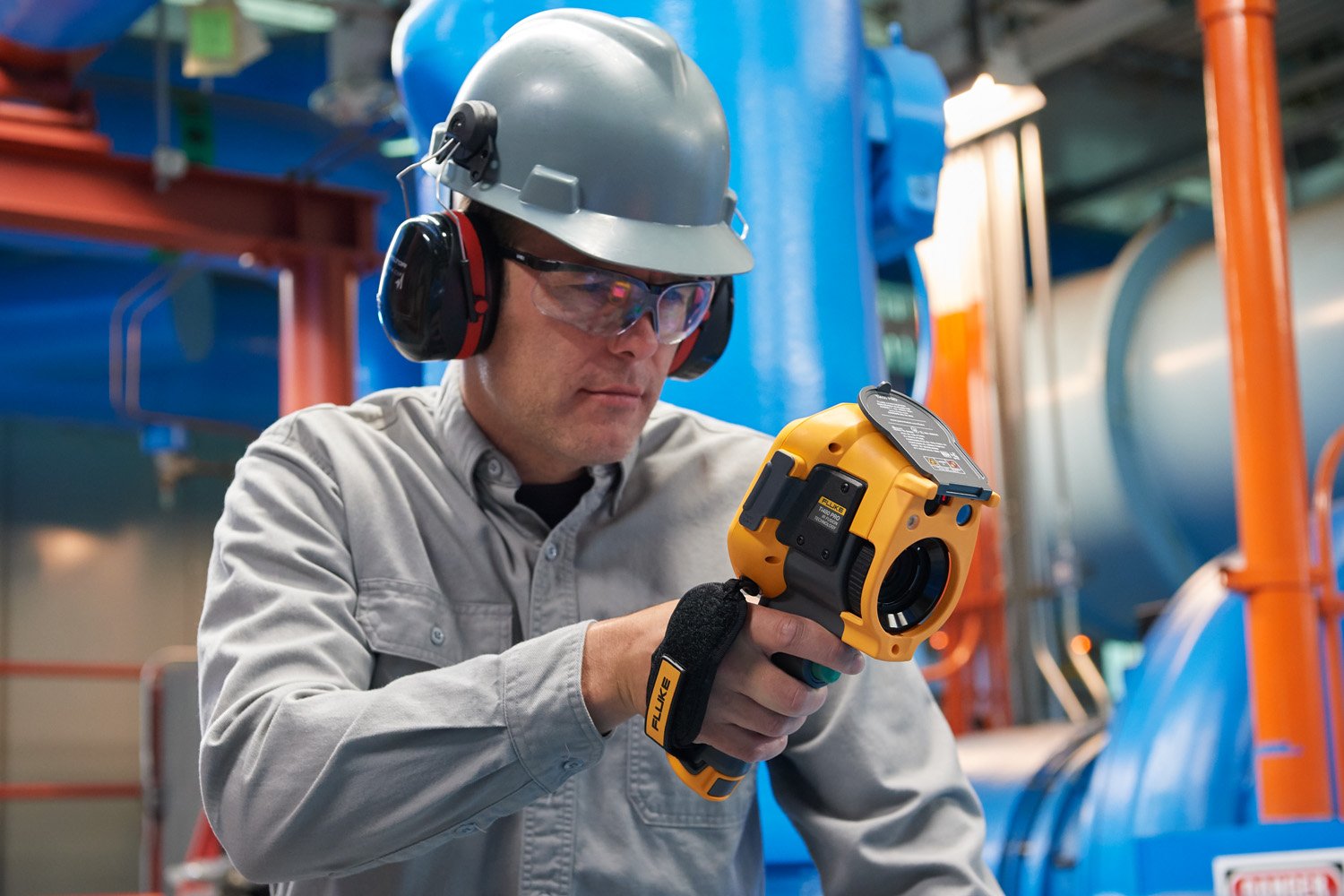
Inspektion mit einer Wärmebildkamera Fluke Ti401 PRO
Eine Wärmebildkamera kann auch zur Erkennung von Dampflecks verwendet werden. Suchen Sie nach lockeren oder fehlenden Dämmungen, und prüfen Sie die ordnungsgemäße Funktion aller Kondensatabscheider. Reinigen Sie die Heizkessel von innen und prüfen Sie die Dampfübertragungsleitungen auf Blockierungen. All diese Maßnahmen zusammen helfen Ihnen zu erkennen, wo Energie verschwendet wird, und helfen dem Team bei der Planung von Energiesparlösungen – von denen viele häufig durch Instandhaltungsmaßnahmen statt über Kapitalausgaben umgesetzt werden können.
Druckluft
Ein Luftverdichter mit 75 kW kann etwa 50.000 € an Energiekosten im Jahr verbrauchen. 30 % dieser Elektrizität gehen in die Erzeugung von Druckluft, die aufgrund von Lecks in der Verteilung und verschwenderischen Nutzungsgewohnheiten nie genutzt wird. Viele Betriebe haben die Effizienz des Druckluftbetriebs jedoch nie analysiert. Dadurch investieren sie in einen zusätzlichen Verdichter, wenn mehr Luftdruck benötigt wird, und betreiben diesen, ohne jemals zu erkennen, dass sie bereits mit dem installierten System mehr Druck erzeugen könnten.
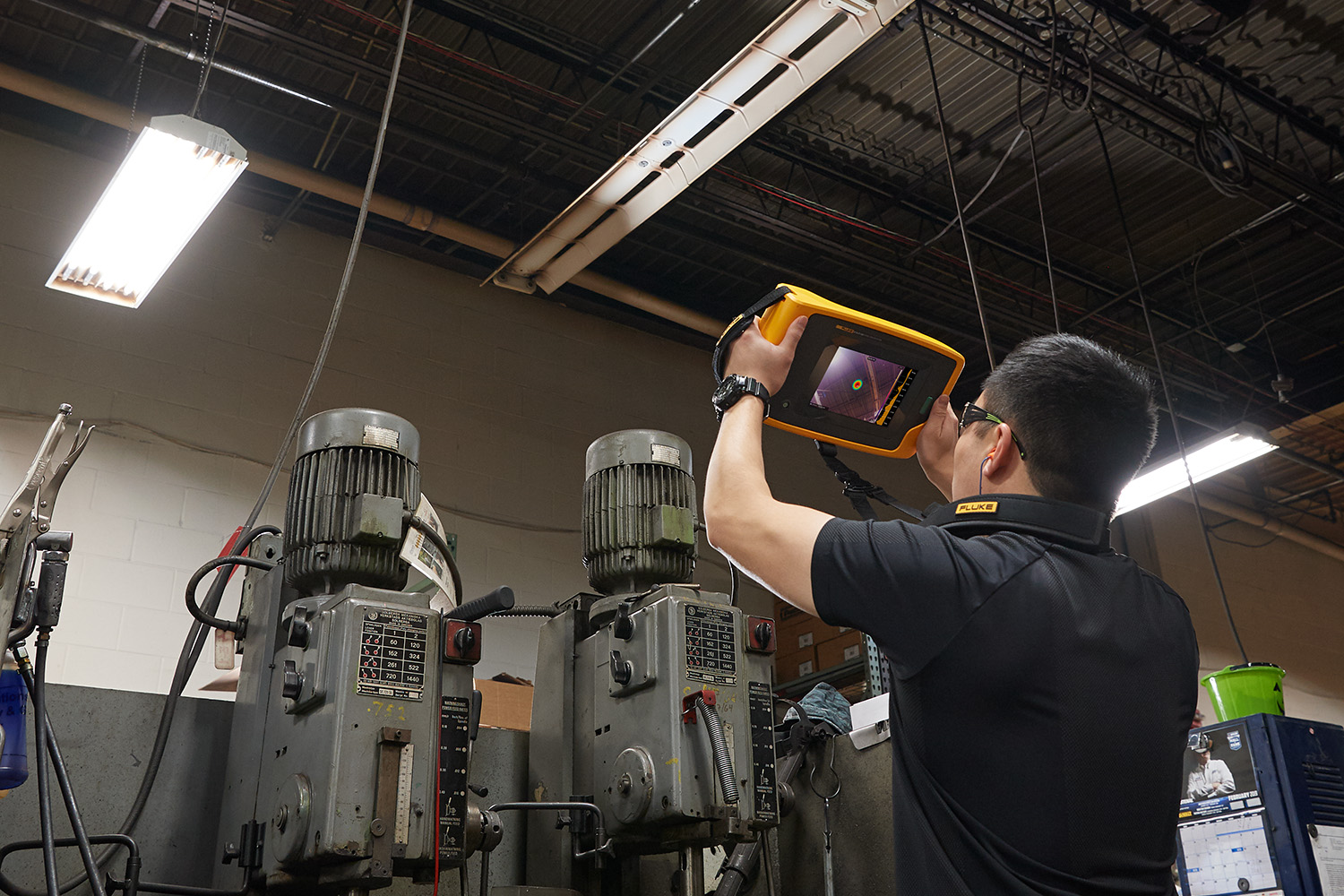
Inspektion von Druckluftleitungen mit der Industrie-Schallkamera Fluke ii900
Studien im Rahmen der Compressed Air Challenge ergaben, dass nur 17 % der Nutzer von Druckluft die Effizienz als Managementziel für Druckluftanlagen bewerten, jedoch 71 % einfach eine konsistente, zuverlässige Luftversorgung liefern möchten. Dieser sorglose Umgang lässt sich bis hin zum Einsatzort beobachten: Installationen pneumatischer Maschinen fehlt es häufig selbst an einfachen Absperrmagnetventilen, was zu einem kontinuierlichen Betrieb des Verdichters führt, und Fertigungsmitarbeiter behandeln Druckluft häufig wie eine kostenlose Ressource, verwenden sie zum Reinigen des Arbeitsbereichs oder sogar, um sich abzukühlen.
Um das Maß der Verschwendung zu erkennen und zu quantifizieren, sollten Sie zunächst an allen Luftverdichtern die Leistung über einen vollen Betriebszyklus protokollieren. Auf diese Weise können Sie feststellen, wie viel Energie zur Erzeugung des Druckluftpegels im zeitlichen Verlauf benötigt wird. Protokollieren Sie außerdem mit einem Präzisions-Manometer den Druck am Verdichterausgang im Vergleich zum Einsatzort, ermitteln Sie den Betrag des Druckabfalls und überprüfen Sie den vom Hersteller angegebenen Druck, der für den Betrieb von pneumatischen Maschinen benötigt wird. Stellen Sie nicht „einfach so“ einen Überdruck her. Ein Multimeter mit Datenprotokollierung, an das ein Druckmodul angeschlossen ist, bietet eine Möglichkeit zur Durchführung dieser Messungen, ohne in Spezialgeräte investieren zu müssen. Verwenden Sie schließlich eine Industrie-Schallkamera für eine möglichst umfassende Untersuchung der Luftleitungen, um Ort und den Umfang von Luftlecks zu ermitteln. Ermitteln Sie Ihre Rendite mit diesem Luftleck-Rechner.
Fazit
Letztendlich können Sie mit diesen einfachen und bewährten Verfahren große Fortschritte in der Energieeffizienz in ihren Anlagen und Gebäuden erzielen. Schon für sich allein genommen bietet jedes dieser Verfahren einen Mehrwert, aber in der Kombination können sie zu hohen Energieeinsparungen führen.