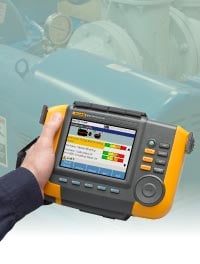
Viele Betriebe arbeiten noch mit einer Instandhaltungsstrategie, bei der die Geräte laufen, bis ein Ausfall stattfindet. Hier wird nichts unternommen, bis ein Gerät kaputt geht, und die Mitarbeiter des Instandhaltungsteams rennen von einem Desaster zum anderen. Die Instandhaltungskosten und Produktionsverluste sind hoch.
Manche Betriebe sind zu einer vorbeugenden bzw. zeitbasierten Instandhaltungsstrategie übergegangen. Es werden Arbeiten durchgeführt, egal in welchem Zustand sich die Ausrüstung befindet. Bei dieser Methode werden einwandfrei funktionierende Maschinen unnötigerweise repariert, was wiederum zu einer Kostenerhöhung führt.
Während der letzten 30 Jahre sind die US-Marine und viele der Fortune-500-Unternehmen von vorbeugender Instandhaltung zu zustandsorientierter Instandhaltung übergegangen. Bei zustandsorientierter Instandhaltung werden Maschinen durch Methoden wie Schwingungsanalyse geprüft, wobei ein Gerät nicht gleich auseinandergenommen werden muss, um dessen Zustand zu bestimmen. Bei einem Fehlerzustand wird eine Reparatur erst dann durchgeführt, wenn sie benötigt wird und nicht vorher oder nachher.
Frühe Anzeichen des Maschinenzustands
Zur Prüfung und zur Diagnose eines Maschinenzustands werden verschiedene Technologien verwendet. Zwei der am meisten verbreiteten Prüfverfahren sind Schwingungsprüfungen und Infrarot-Thermografie. Die Kurve verdeutlicht, wie Veränderungen zuerst mit Schwingungstests und dann mit Infrarot-Thermografie erkannt werden können. Nur zu einem späteren Zeitpunkt – kurz vor Ausfall der Maschine – machen sich Schäden akustisch bemerkbar und es entsteht Überhitzung.
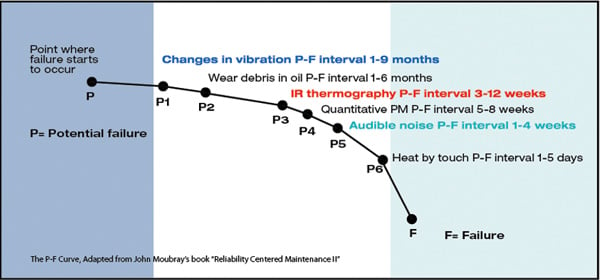
Vorteile von Schwingungsmessungen sind unter anderem:
- Vorhersagbarkeit. Instandhaltungsmitarbeiter können Reparaturen planen und die benötigten Teile einkaufen.
- Sicherheit. Fehlerhafte Ausrüstung wird aus dem Verkehr gezogen, bevor Gefahren auftreten.
- Einsparungen. Gut gewartete Maschine haben weniger unerwartete oder schwerwiegende Ausfälle und helfen so, Produktionsstopps zu verhindern, die sich negativ auf den Umsatz auswirken.
- Verlängerte Wartungs- und Instandhaltungsintervalle. Die Lebensdauer der Ausrüstung wird verlängert und Instandhaltungen werden nach Bedarf durchgeführt.
- Zuverlässigkeit. Bei der Ausrüstung entstehen weniger unerwartete bzw. kritische Ausfälle, da Problembereiche vor der Störung schon bekannt sind.
- Seelenfrieden. Größeres Vertrauen in Instandhaltungspläne, Budgetplanung und Produktivitätsschätzungen.
Mechanik der Schwingungsmessung
Ein Messwandler erfasst Schwingungssignale von den Lagerpositionen und überträgt sie an einen Datensammler. Es folgen einige wichtige Hinweise zur Beachtung bei der Mechanik der Schwingungsmessung:
- Durch rotierende Ausrüstung wird ein eindeutiges Schwingungssignal erzeugt, ein Attribut.
- Diese einzigartigen Signale werden normalerweise nacheinander aufgenommen, wobei die Amplitude des Signals (y-Achse) als Funktion der Zeit (x-Achse) dargestellt wird. Dabei handelt es sich um eine zeitabhängige Signalform.
- Die Signalform enthält Informationen über die Maschine zum Zeitpunkt der Messung. Schwingungen werden von rotierenden Wellen, nahe gelegenen Maschinen, Fundamenten, Lärm, rotierenden Komponenten, strukturellen Resonanzen, Strömungsturbulenzen und anderen Quellen erzeugt.
- Hier arbeiten jedoch verschiedene Faktoren zusammen und überschneiden sich. Eine klare Trennung der einzelnen Schwingungssignale ist kompliziert.
- Eine im Datensammler durchgeführte Frequenzananlyse vereinfacht die Signalform und zerlegt sie in bestimmte Wiederholungsmuster. Fast-Fourier-Transformation (FFT) ist die Bezeichnung für einen mathematischen Algorithmus, der über das Schwingungstestgerät an den einzelnen Schwingungssignalen durchgeführt wird.
- Als Spektrum wird die Darstellung all dieser Einzelsignale auf einer einfachen Kurve mit Amplitude (y-Achse) und Frequenz (x-Achse) bezeichnet.
Wir können dies in einem Drei-Schritte-Prozess vereinfachen.
- Schwingungsspitzen identifizieren, da diese sich auf eine Quellkomponente der Maschine beziehen.
- Muster identifizieren, die auf der Datengrundlage der Schwingungsbedingungen beruhen.
- Amplitudenmessung der Schwingungsspitzen, um den Schweregrad der Störung zu ermitteln.
Sobald die Störung und der Schweregrad ermittelt wurden, kann eine Reparatur und ein Arbeitsauftrag empfohlen werden.
Lagerstörungen und -ausfälle
Eine Studie der SKF-Group untersuchte die Lebensdauer von 30 identischen Lagern und kam zu dem Ergebnis, dass ein hoher Unterschied bei der Lebensdauer auftrat. Somit wird die Anwendung eines effektiven Instandhaltungsprogramms aufgrund von Zeitintervallen ausgeschlossen.
Eine andere Studie kam zu dem Ergebnis, dass Lagerstörungen die Ursache von mehr als 60 Prozent mechanischer Störungen sein können. Obwohl Lager erheblich an mechanischen Störungen beteiligt sind, sind die eigentlichen Lagerstörungen das Resultat eines separaten und latenten Problems, wie zum Beispiel Unsymmetrie. Manche Kunden tauschen Lager in monatlichen Abständen aus, bis sie gelernt haben, die Maschine zu stabilisieren und auszugleichen – danach halten die Lager jahrelang. Lager versagen aufgrund von:
- schlechter Isolierung
- schlechter Schmierung
- Verschmutzung
- Verschleiß und Materialermüdung
- anderen Störungen
Ein Wälzlager – auch Rollelementlager – trägt eine Last, indem runde Elemente zwischen zwei Gegenständen platziert werden. Heutzutage sind in den meisten Maschinen Wälzlager eingebaut.
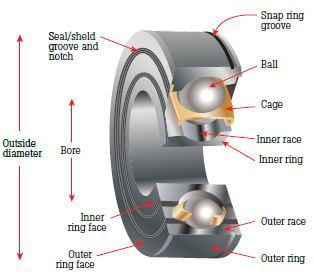
Defekte bei Wälzlagern
Lagerfrequenzen sind asynchron. Die Geometrie von Kugeln, Käfigen und Laufringen wird bei unterschiedlichen Drehzahlen deutlich; diese Drehzahlen entsprechen nicht einem Mehrfachen der Wellendrehzahl. In der Regel handelt es sich bei asynchronen Spitzen um Wälzlager. Die meisten Schwingungsprogramme verwenden die folgenden Lagerfrequenzen:
- innerer Laufring
- äußerer Laufring
- Käfig
- Kugelumlauf
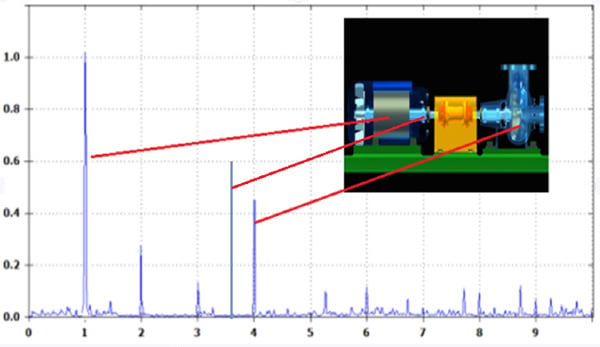
Die Kurve verdeutlicht ein Datenbeispiel einer Lagerstörung. Beachten Sie, dass die Schwingungsspitze von der Welle der einfachen Wellendrehzahl entspricht (Drehzahl von 1,775 U/min). Im System befinden sich vier Laufradschaufeln und sieben Lüfterflügel. Eine starke Schwingungsspitze entsteht bei der 3,56-fachen Wellendrehzahl. 3,56-Laufradschaufeln und 3,56-Lüfterflügel sind unmöglich.
Die neun Stufen beim Lagerverschleiß
Es existieren mehr als 4.700 Regeln zu Maschinenstörungen. Diese Regeln basieren auf der Musteranalyse von Maschinenwellen und sie sind in die Diagnoseroutine des Schwingungsmessgerät Fluke 810integriert. Die häufigsten Defekte sind Unsymmetrie, Fehlausrichtung, Lockerung und Lagerprobleme. Die unten aufgeführten neun Stufen verdeutlichen die Änderung des Musters bei fortschreitendem Lagerverschleiß.
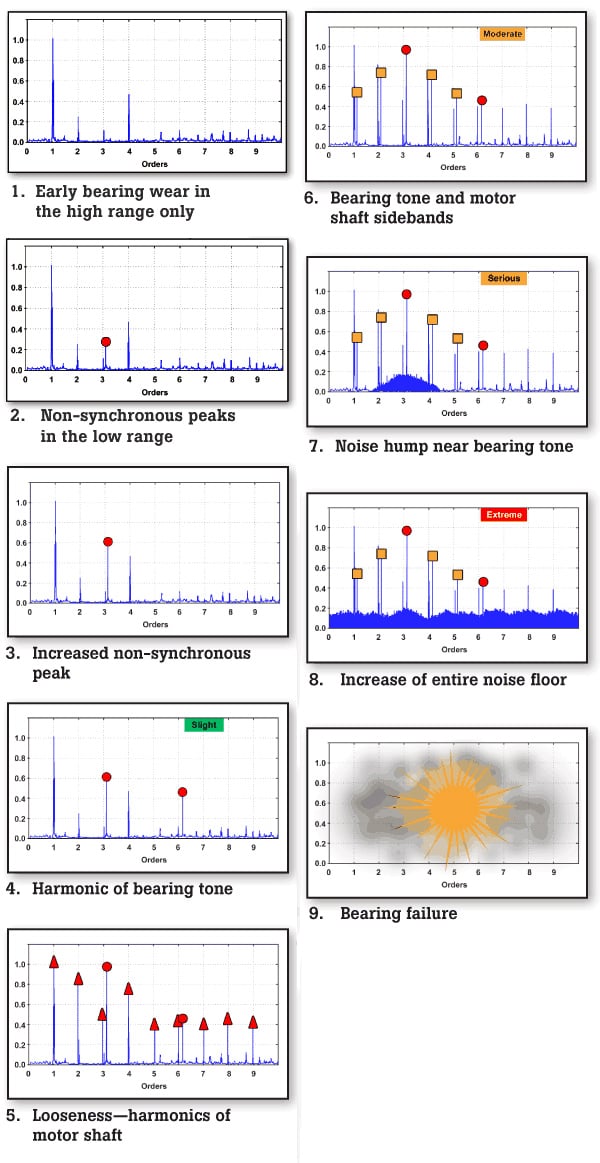
Wie kann ein Schwingungsanalytiker fehlerhafte Lager feststellen? Der Analytiker untersucht komplexe Signale. Das Training für die Signalformanalyse dauert Jahre und es bedarf jahrelanger Erfahrung, um sich für diese Untersuchungen zu qualifizieren. Es existiert noch ein anderes Verfahren, es ist jedoch sehr zeitaufwendig: Man muss Kontakt mit dem Lagerhersteller aufnehmen und eine Tabelle mit den Lagerfrequenzen anfordern. Mit der Tabelle können dann die Frequenzen überlagert werden und man kann prüfen, ob die Daten für die asynchronen Spitzen mit denen der Tabelle übereinstimmen. Wenn sie übereinstimmen, dann wurde die Störung am Lager gefunden. Wenn sie nicht übereinstimmen, dann ist es wahrscheinlich, dass es sich um ein anderes als das angegebene Lager handelt. In einem solchen Fall muss herausgefunden werden, ob das Lager gegen ein Lager eines anderen Herstellers ausgetauscht wurde, ohne die Wartungsprotokolle zu aktualisieren. Das einfachste Gerät zur Schwingungsmessung ist der Schwingungsmessstift. Mit einem Schwingungsmessstift können spezifische Variablen wie Lagerzustand und -temperatur gemessen werden. Bei einer höheren Geräteklasse kommt ein Schwingungsmessgerät zum Einsatz, mit dem der Wert für die Gesamtschwingung sowie spezielle Variablen gemessen werden können. Das Schwingungsmessgerät Fluke 805 bietet eine kombinierte Schwingungs- und Kraftsensorspitze, mit deren Hilfe die vom Benutzer verursachten Abweichungen (bezüglich Kraft oder Winkel) ausgeglichen und somit exakte, wiederholbare Ergebnisse erzielt werden können. Dieses Messgerät verfügt über eine vierstufige Skala für den Schweregrad und einen integrierten Prozessor zur Messung des Lagerzustands und der Gesamtschwingung. Die entsprechenden Ergebnisse werden anhand leicht verständlicher Textmeldungen angegeben (Gut, Befriedigend, Unbefriedigend, Inakzeptabel). Die Sensoren sind für das Auslesen eines großen Frequenzbereichs konzipiert (10 bis 1.000 Hz und 4.000 bis 20.000 Hz) und decken somit die meisten Maschinen- und Komponententypen ab. Zudem verfügt das Modell 805 über eine selbsterklärende Bedienoberfläche, mit der die Benutzereingaben hinsichtlich des Drehzahlbereichs und des Gerätetyps minimiert werden. Hiermit verfügen Instandhaltungspersonal und Bediener über ein Prüfwerkzeug, mit dem festgestellt wird, welche Komponenten ordnungsgemäß funktionieren und bei welchen eine zusätzliche Fehlersuche durchgeführt werden muss. Wie schon oben beschrieben, verfügt das Schwingungsmessgerät Fluke 810über eine Diagnoseroutine, mit der Algorithmen mit einer Datenbank von Messwerten aus dem Praxisalltag kombiniert werden.
Herkömmliche LageranalyseSchwingungsmessstift, Messgeräte und Tester
Weitere Informationen