Keeping plants up and running at maximum efficiency and with minimum unplanned downtime is the goal of every maintenance team. Achieving those levels of uptime requires maintaining assets in such a way that it allows you to catch a problem before it takes down your operation. The question is how best to do that.
Historically, most plants have operated with a reactive maintenance strategy—running to failure and then fixing the equipment when it breaks down. That can be very costly in downtime, wasted product, shorter equipment life cycles, and increased equipment replacement and labor costs.
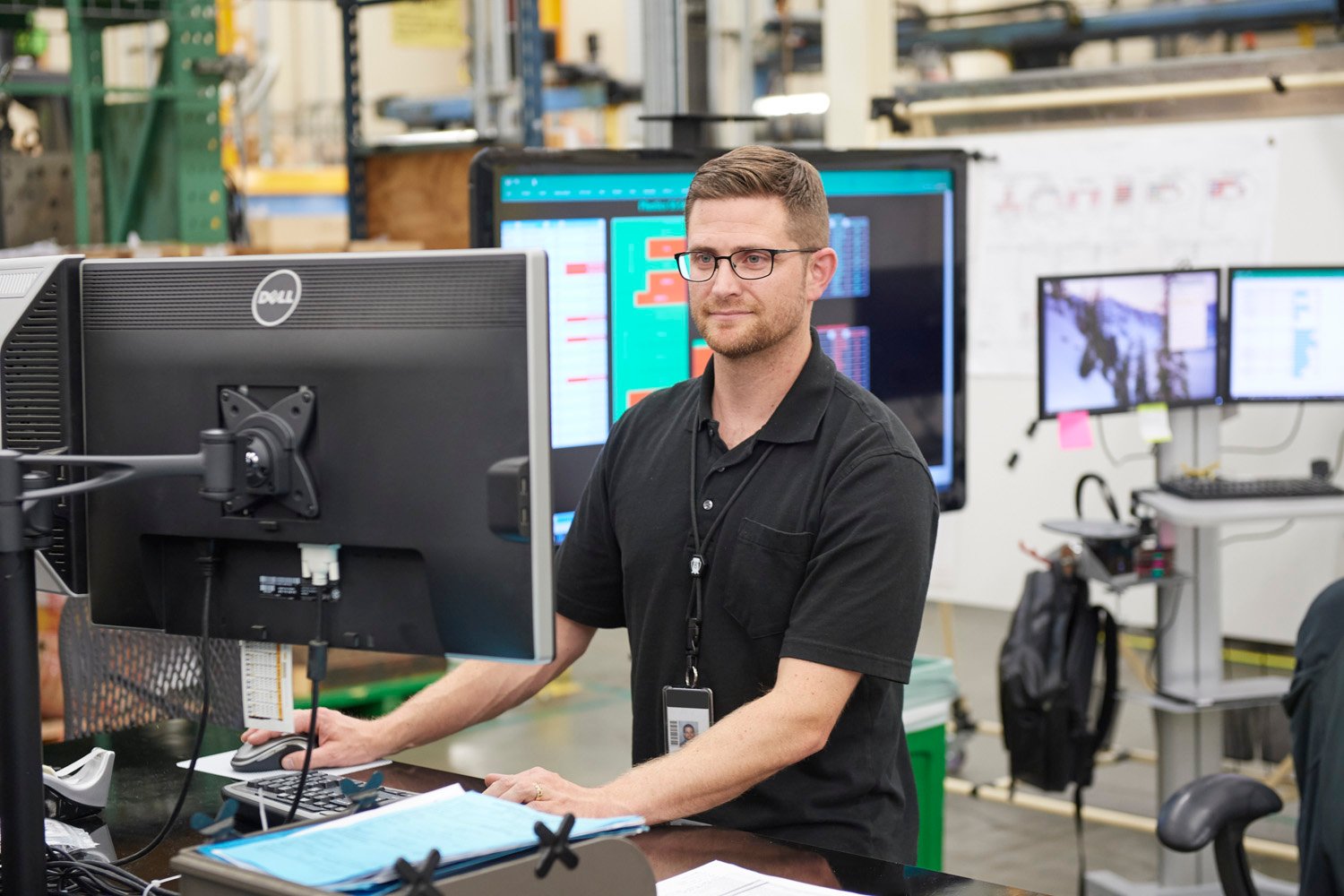
Many plants still use some level of reactive maintenance. But industrial equipment has become more automated, and troubleshooting and diagnostic tools have become more available, accurate, and affordable. Today, more and more industrial plants have started taking a proactive approach to maintenance. The immediate goal is to find and fix problems before there’s a breakdown. The long-term goal is to reduce unplanned outages and extend asset life.
Preventive maintenance reduces risk
One alternative to reactive maintenance is preventive maintenance, which establishes a regular maintenance schedule for each machine. This helps reduce equipment failure and extend equipment life, but it also is labor intensive. Preventive maintenance intervals are typically based on recommendations from equipment manufacturers rather than on specific data related to each machine. That can lead to excessive maintenance and unnecessary component replacement based solely on time, rather than on the actual condition of the component. This approach also requires shutting down the equipment, which can have a negative impact on production. Still, preventive maintenance has proven more cost effective than reactive maintenance because, in addition to reducing unplanned downtime, it also saves energy by keeping equipment running more efficiently.
Predictive maintenance sees around corners
Predictive maintenance is sometimes confused with preventive maintenance in that it is designed to address potential equipment problems before they cause a breakdown. However, rather than performing maintenance tasks based strictly on time intervals, predictive maintenance uses real world data from the equipment to determine when and what to perform maintenance on. It applies algorithms to that data to find trends in key indicators, such as temperature, vibration, electrical, pressure, and other measurements that can indicate when a failure is likely to happen.
Much of the data used in these calculations is collected in real time with infrared technology and wireless or wired condition monitoring sensors while the equipment is running. This helps create a more accurate and comprehensive picture of both individual assets and the health of the operation as a whole.
Building a proactive maintenance program
Predictive and preventive maintenance approaches work together to influence a proactive maintenance strategy. By collecting baseline data, tracking trends, and analyzing data after fault indications are found, a proactive maintenance strategy helps organizations perform maintenance only when necessary, based on real world information. It can also help make predictive and preventive maintenance programs work more efficiently to help avoid the root causes of machine failure, address problems before they cause failure, and extend machine life.
The biggest challenge in establishing a proactive maintenance program is determining how best to direct your maintenance resources. Analyzing the data from both healthy and faulty equipment can help you determine when a piece of equipment may fail. But, because most organizations have limited maintenance resources, the next challenge is to decide which failures pose the biggest risk to your operation.
How to assess maintenance priorities
So, in addition to collecting performance data, it is helpful to assess the criticality of each asset. Rather than simply rating assets as “critical” or “non-critical” you can classify your assets into four categories of criticality based on the impact of that asset on the company’s ability to generate revenue. Those four categories are:
- Star Athletes, which are assets that directly determine your organization’s ability to win, and by how much. In addition to simple uptime and downtime, there’s a direct relationship between performance and revenue to your company. Every bit of performance improvement means additional revenue. These assets need constant attention and monitoring, regardless of their age. Examples include turbine generators, large ship engines, and large process kilns and furnaces. Basic manufacturing plants may have few or no assets in this category. Continuous process industries often have many interconnected star athlete assets.
- Critical assets are those that must be up and running in order for your company to make money. In the case of municipal services, public facilities, or non-profit organizations, or others that don’t generate revenue, these assets must be running to fulfill the organization’s mission, operate within budget, or provide the expected level of service. Performance is less of an issue. If things are spinning, conveyors are moving, or hydraulics are actuating, the assets can help your organization make money. Uptime is the key performance indicator so it is critical to be able to anticipate pending failures. Note that critical assets aren’t necessarily big and complex. Sometimes a chemical process depends on a simple solenoid valve, or a food processing line depends on whether a $20 motor is dispensing material out of a hopper.
- Semi-critical assets are those that don’t necessarily stop production when they go down but do strain the system. For example, a warehouse or distribution center has four forklifts, and one goes down. Things keep moving, but the remaining forklifts must work 33% faster or longer. Or if an automated rivet press on a production line goes down, the line won’t stop but production personnel will have to pick up the slack by manually driving the rivets. This increases labor costs and slows down production.
- Non-critical assets do not affect the company’s ability to generate revenue—no matter how big, expensive, or complex they may be, but there still may be reasons to fix these assets. For example, if you have a rotating company sign in front of your building that stops rotating or goes dark, you still need to fix it to maintain your company image.
These criticality classifications are just general guidelines. One company’s non-critical asset may be another’s star athlete. It is important that you classify your assets in terms that meet the specific situation in your company and plan your maintenance strategy accordingly.