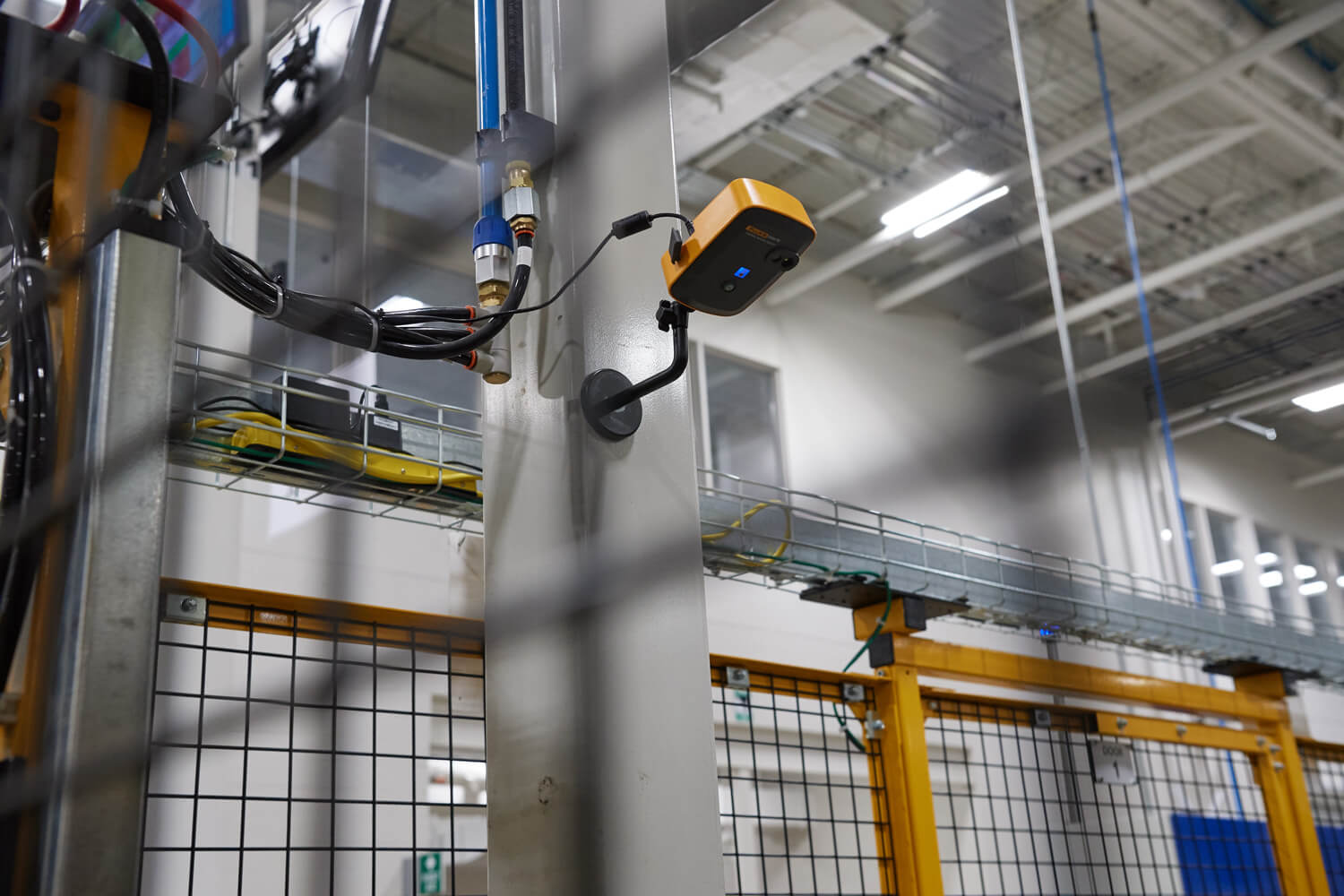
The benefits of proactive maintenance are widely known, so why isn’t it everywhere in the maintenance world? Obstacles include:
- Changing maintenance culture from “preventive” to “predictive” is a slow process.
- Allocating full time resources to learn and perform analysis requires significant investments for setup and training.
- Maintenance teams need more than a year to be trained and get proficient in understanding vibration, which can test a manager’s resolve.
- Often, only companies with processes “critical enough” to affect cost of downtime and safety concerns—such as the petrochemical, power generation, and pulp and paper industries—will implement condition monitoring. Some companies have redundant systems instead of vibration monitoring because of the complexity of their assets.
Do you feel like proactive maintenance isn’t viable for your facility and you have to choose among:
- Changing parts regularly before they wear out
- Outsourcing vibration consultants
- Using primitive techniques to analyze machine condition
- Run-to-fail (high costs and hard to break free from)
Two ways leaders can approach a proactive maintenance program
Idealized approach
A dedicated predictive maintenance (PdM) or reliability team at a large industrial plant with the people, time and budget to do proactive work and identify the most critical equipment in-plant. Such a team would use an automated system/CMMS to monitor equipment and store and track data, which determines when equipment needs maintenance to optimize performance and prevent damage or failure.
The rest of us
A small maintenance team at a mid-sized industrial or large commercial facility with no dedicated people for predictive maintenance, but the best reactive practices they can manage. Such a team would have broad responsibilities, but not the scope or budget to justify going full SCADA or sensors for remote monitoring. They would gather data by hand as the job dictates to get the work done and solve problems as they arise.
Technology has improved to the point where maintenance technicians can use the same techniques and tools to troubleshoot as well as to inspect, log and share—the basics of proactive maintenance.
Top 5 trends in industrial maintenance
- Downtime is getting more expensive. The scale of facilities and commodity costs are increasing as facilities are becoming more specialized.
- Maintenance must do more with less. Workforces are becoming leaner: Experts are retiring but not being replaced. Production demands are up while budgets are continually decreasing. Just-in-time processes are reducing room for error.
- Awareness is quickly growing. The value of maintenance best practices is gaining significant attention from industry influencers and professional associations. Reliability is being discussed in the board room. Maintenance is no longer just a cost to doing business; it is a part of operational excellence and a strategic advantage.
- New maintenance technologies are experiencing mass adoption. Tool prices are falling while performance is improving. Technological advances are making complex tools smarter and easier to use by all technicians—not just experts or specialists. Many industries are seeing a dynamic shift in the ideal mix of outsourced vs. in-house maintenance.
- Companies are increasingly using maintenance best practices to reinforce and extend their competitive advantages. Implementing maintenance best practices can help companies achieve outcomes such as improved process quality and reduced operating costs (including less spending on parts and compliance).