What does measurement have to do with saving energy? It's all about ROI and the bottom line.
Industrial facilities must consume energy to run—product, data, whatever it is—and most plants waste too much electricity. They’re inefficient energy users. Twenty ago, facility management didn't care about energy efficiency—energy was cheap. Once energy became more expensive, managers became interested in reducing their energy bill, but the measures had to be put into business terms.
Where is the ROI conversion point where the waste is great enough that it makes sense to address?
To answer that question, you need to measure how much energy you are consuming on the different types of work (systems) in your building and compare to standards. That tells you how much waste is occurring. Further measurement can help you identify root cause of the waste. The three points of an ROI equation are: 1) the quantity of waste combined with 2) the cause and 3) the cost to address.
When does energy reduction make sense?
Energy reduction makes sense for facilities that want to reduce overhead to increase productivity—facilities that are looking to do more with less, not just spend less.
Energy inspection identifies opportunities to increase efficiency and gives the facility manager the data to understand which energy saving activities make sense given the facility's primary objectives, and which ones either don't offer enough ROI or fall too far outside the priorities. The biggest opportunities typically exist in facilities that have old, large, high-energy-consuming systems that have not been optimized. Other good candidates include production facilities that have not introduced much automation or controls as well as facilities with large steam or compressed air systems.
How much can be saved?
According to the U.S. Department of Energy (DOE),facilities could lower their energy bills by 25 %, but the actual savings depend on a couple of things. First, what kind of systems and activities occur in the facility? Large loads that have never been mapped to the utility rate schedule to take advantage of the cheapest times of day have the promise to deliver significant savings. A facility running mostly smaller loads may not see the same opportunity. Second, how inefficient are the building systems? A newer, well-maintained facility isn't going to offer as many savings opportunities as an older facility where systems and equipment have drifted from recommended settings and maintenance practices.
When you think about energy waste at home, you likely think about cold air leaking in through the window or replacing old light bulbs with LEDs. But what kind of "energy waste" occurs in a manufacturing or mixed-use facility?
Using energy to heat or cool air and force it through the ventilation system, only to leak it out the window, forces the system to over-produce, and therefore overconsume. How many other systems in the facility are working harder than they should, due to clogged filters, oversized motors, and so on?
So, yes, a manufacturing or mixed-use facility may experience both lighting and building envelope wastes. But are those the first wastes to address?
You can't answer that question until you log power consumption at all the major loads, map it to both the rate schedule and the operational schedule, and do the ROI math. Quite often, a facility will uncover enough maintenance and operational savings on large equipment that within a few years they've saved enough money to accelerate the equipment replacement with a leaner model.
How to start reducing energy consumption when budgets, time, and resources are all limited
Work from a baseline.
The place to start is identifying where—and when—energy is being used, by what. Once facility owners, managers, and technicians understand exactly how much energy is required to run the business, versus how much energy is being wasted, then they can make decisions and build a plan. To get to that state, start by getting copies of the last several utility bills and look for signs of penalties and peak demand charges. Download a copy of the rate schedule from the utility website, so that you know how much energy units cost at different times of day, compared to your operational schedule. If necessary, call the utility service department directly; they will be happy to hear from you.
Then, either instruct your own electrical team or an electrical contractor to log power at the main utility service entrances as well as at the supply panels to the largest systems and loads. Record kW, kWh, and power factor over a representative period. This provides a very accurate picture of the actual power consumption on three-phase circuits and loads. The biggest savings often come from shifting load operations to cheaper energy times of day.
Which systems are the biggest energy wasters?
Aside from mapping the electrical supply system, evaluate your electromechanical, steam, and compressed air systems. They are usually rife with wasted energy usage, but with fairly easy fixes.
Electromechanical
There are five common types of energy waste in an electromechanical system: 1) electrical, 2) mechanical/friction, 3) scheduling, 4) controls, and 5) sizing/efficiency.
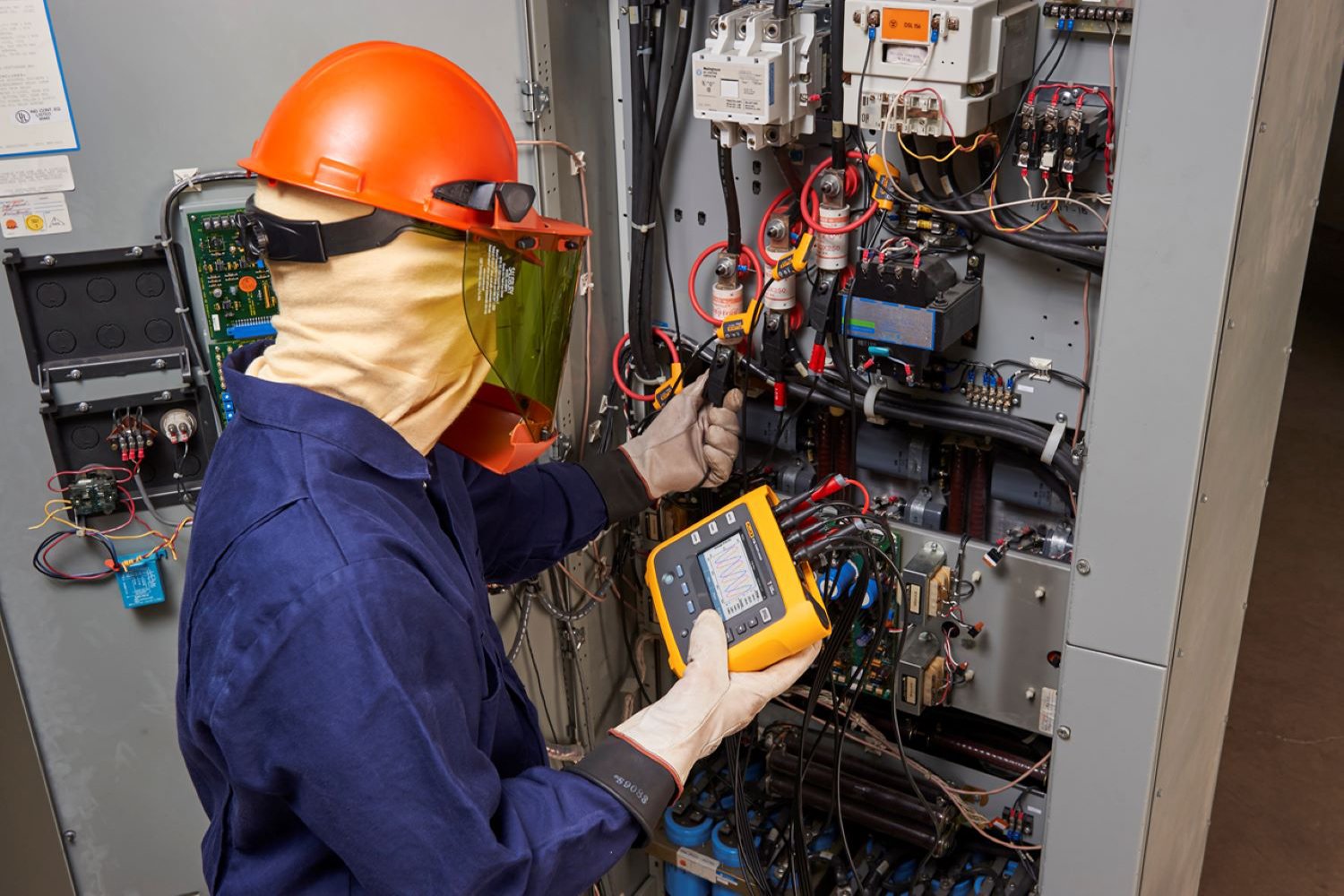
Using a Fluke 1738 Advanced Power Energy Logger to perform an energy study on a mechanical system
- Voltage/current overload and phase unbalance are two top energy wasters in electromechanical systems. Both of these electrical issues can be detected with power quality analyzers and thermal imagers.
- Energy-wasting mechanical situations manifest as both overheating and excess vibration, detectable with thermal imaging and vibration meters. Possible causes vary, from cooling and airflow to bearing alignment and other causes of friction. Thermally scan couplings, shafts, belts, bearings, fans, electrical components, termination/junction box, and windings—all things that can signal inefficient operations, and thus waste energy.
- As alluded to earlier, one of the easiest energy savings solutions is to log power consumption at large electromechanical loads over a full operational schedule. Determine when the machinery uses the most energy (often at startup) and check whether usage times can be adjusted to times of the day when utility rates are the cheapest.
- Using that same power log, compare the operational schedule to how often the machine uses energy. How much power is it using when not in active use? Without the use of controls, most machinery must be manually turned off to stop consuming energy, and manual actions don't always occur. Not all machinery can be feasibly turned off, but most can be idled. Controls vary from simplistic to fully automated; and from using sensors and timers to flexibly idle machinery to hard-coding operations into a PLC.
- Sizing and efficiency rating. In older facilities especially, operational requirements change but the loads stay as is, meaning that sometimes a large, expensive, hard-start motor is left driving a less horsepower-intensive system. The natural inclination of any facility manager is to get the maximum lifetime out of a large piece of equipment. However, it's worth logging how much power the motor uses, compared both to actual load requirements as well as to a new, high-efficiency, right-sized unit. Calculate how much excess energy is being consumed and multiply by the rate schedule. Determine how long a new motor would take to pay for itself: sometimes it makes financial sense to replace equipment before it fails. If not, consider whether controls could be used to modulate output.
Steam
Process heating accounts for a sizeable portion of controllable operating costs and the system must be regularly inspected to avoid several different energy-wasting scenarios.
To begin, log energy consumption at the boiler to get a baseline for energy consumption. Then, inspect the distribution system, including steam traps, pressure gauges, insulation, pumps, and valves. Use a thermal imager to detect failed steam traps, leaks, blockages, value issues, and condensate failures: the goal is to return as much preheated condensate to the boiler as possible.
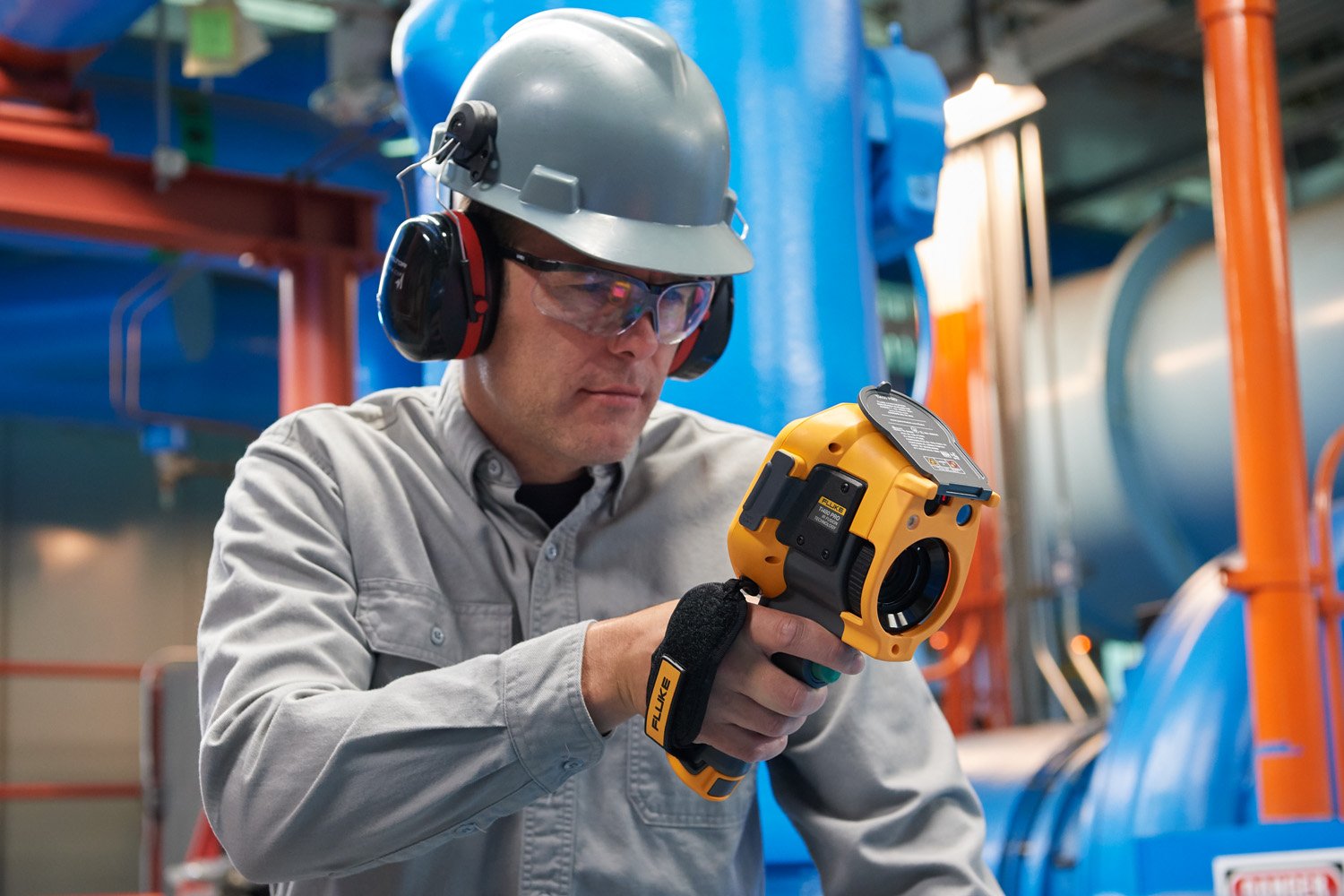
Fluke Ti480 PRO Infrared Camera
A thermal camera can also be used to check for steam leaks. Be sure to check for loose or missing insulation and proper operation of all steam traps; clean inside boilers and check steam transmission lines for blockages. These combined efforts identify energy wastes and help the team plan energy-saving solutions—many of which can often be implemented via maintenance rather than capital expense.
Compressed air
A 100-horsepower air compressor can consume around $50,000 in electricity annually and as much as 30 % of that electricity goes to pressuring air that is never used due to distribution leaks and wasteful usage practices. However, many facilities have never assessed the efficiency of their compressed air operation. In fact, when more air pressure is needed, many facilities will purchase and operate an additional compressor without ever realizing they could get more pressure out of their existing system.
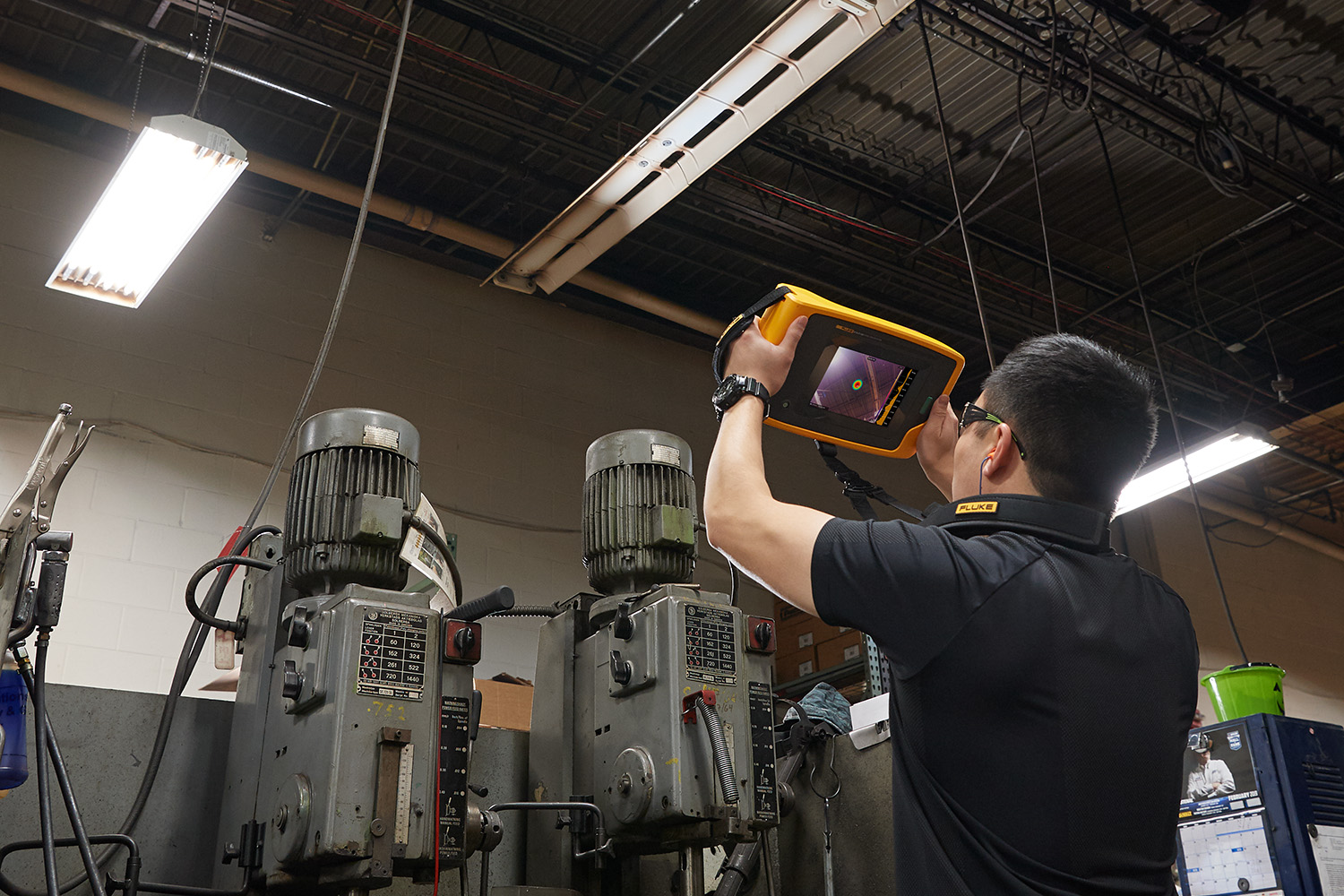
Inspecting compressed air lines with the Fluke ii900 Sonic Industrial Imager
Studies by the Compressed Air Challenge found that only 17 % of compressed air users value efficiency as a compressed air system management goal, yet 71 % simply want to deliver a consistent reliable air supply. That philosophy transfers down to the point of use: pneumatic equipment installations frequently lack even simple solenoid shut-off valves, driving continuous compressor operation, and shop floor personnel often treat compressed air as a free resource, using it to clean the work area and even to cool off.
To identify and quantify the level of waste, start by logging power over a full business cycle at all air compressors. This will establish how much energy it takes to produce current air pressure levels. Also, use a pressure gauge calibrator to log the psi at the compressor output compared to the point of use, determine the amount of pressure drop, and verify manufacturer psi required to operate pneumatic equipment; don't over-pressurize "just because." A pressure module plugged into a logging multimeter is one way to conduct these tests without investing in specialized equipment. Finally, use a sonic industrial imager to scan as much of the air-line footprint as possible, to determine the location and scope of air leaks. Find out what your ROI is using this air leakage calculator.
Conclusion
Ultimately, you can make great strides to improve energy efficiency at the plant level with these simple and straight forward best practices. Individually they will provide value, but when combined, they can become a power house of energy savings.