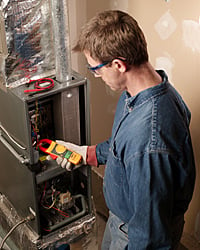
After years of being a serviceman - slinging ladders, dragging tools across attics and through crawlspaces, standing in all sorts of weather on rooftops - I can now leave the service work to one of the younger techs with better knees and concentrate on my primary job as company start-up man. After new equipment is installed, I make sure the system is operating efficiently as designed, count the parts and pieces used on the installation in order to accurately track costs, make sure the customer understands the controls and operation, and pick up the final payment. This has gone a long way in reducing the number of warranty performance complaints, improving our pricing structures, almost eliminating overdue account receivables, and enhancing our reputation.
Customer Profile
Take this job: a furnace replacement in a 25-year-old two-story colonial-style home. We replaced the natural draft gas furnace with a two-stage, energy-efficient direct vent condensing natural gas furnace equipped with a variable speed blower. We also added a zone control panel designed to operate with a variable speed motor that supplies the correct air volumes to each zone (two zones each for the first and second stories of the house) without the need for a bypass damper. Additionally, we installed a two-stage condensing unit, evaporator, heat recovery ventilator, humidifier, and state of the art air purifier.
Tools
Today, I'm on site to make sure the new systems we installed are performing at peak efficiency - and looking forward to trying out my new Fluke 902 HVAC Clamp Meter. I've always enjoyed keeping pace with the latest technology in multimeters and currently use a Fluke 87V with several temperature accessories and an amp clamp transducer for times when I want true-rms amp readings. When it's time for serious work and diagnostics, I'd be lost without it. But with features like True RMS AC volts and amps, DC volts, microamps, temperature, capacitance, ohms and continuity beeper, the Fluke 902 could become my everyday meter.
Systems check
It makes sense to start in the basement with the furnace so the house has more load by the time I'm ready for the air conditioner start-up. I'll record all my readings on a start-up form, and leave a copy in the equipment document bin for the service technician to reference during annual maintenance calls. The other copy will be filed with the job jacket at the office.
I measure and record externals first: gas pipe sizing, vent size and equivalent length, electrical wiring including good quality ground from furnace to service panel. I'm anxious to put my new clamp meter through all of its paces, so I start by checking the capacitor on the combustion air blower and measure 7.2 microfarads. It's within 10 % of its 7.5 MFD rating, so it's fine. I measure and record 123 volts to the furnace and 28 volts on the transformer secondary. I connect my manometers to the inlet and manifold side of the gas valve. I check the static gas inlet pressure and record 6.5" WC (water column). I'll watch for a pressure drop when the gas valve opens.
Electronics can perform erratically, or not at all, if there is not a good ground path back to the source. To check for adequate ground, I set the clamp meter for ac volts and measure from cabinet ground to the line voltage neutral connection on the ignition control. With nothing on the furnace operating, this value should be less than two volts; otherwise the ground circuit will need to be improved. I measure 0.4 volts, so it's okay.
Now it's time to see some operating values. I put the zone panel in central mode and call for maximum system air flow. My incline manometer shows 0.35" WC external static pressure with a dry evaporator. I attribute the reasonable static pressure to the duct improvements we made. I check the blower motor amp draw. The manufacturer of the electronically-commutated motor specifies that amperage must be taken with a true-rms meter. My new clamp meter fits that specification and measures 5.1 amps on a motor rated at 7.7 amps full load. Out of curiosity, I remove the blower door panel and watch my amps drop to 4.8 amps. If this had been a PSC (permanent split capacitor) motor, I would have seen an increase in amps. But these variable speed motors only use as much torque and RPM as they need to achieve required air flow, so less duct restriction means lower RPM at less torque, thus less amperage. I set my clamp meter to volts dc and check the variable voltage demand from the zone panel to the furnace. A reading between 0 volts dc and 22 volts dc would operate the blower proportionally between its factory-default minimum air flow and the field selected maximum flow. I read 22 volts dc; telling me the motor is being commanded to the maximum air flow selected for this system based on cooling capacity (0 volts dc would command the blower to its minimum flow.)
I remove the call for full operating air flow, unplug the hot surface ignitor and measure 15 ohms through it. This particular ignitor should be between 11 and 20 ohms, so it's okay. I reconnect the ignitor and establish a call for a heating demand. I connect my clamp meter across the hot surface ignitor leads to check ignitor volts. This ignition control will reduce ignitor voltage by 6 % on each successive ignition trial until it reaches a "no light" voltage, then it steps voltage back up 6 % and remains there for the next 255 heat cycles. The life of the ignitor is extended if it uses only the minimum voltage; higher voltage produces greater ignitor temperature. The ignition control "conditions" the line voltage, which requires that it be measured with a true-rms meter. I measure 92 volts as the ignitor heats. If I had measured this with a standard averaging meter, my reading would have been deceptively low, probably around 50 volts. I record all of these values on my start-up form as I wait for the gas valve to open.
When the gas valve opens, the gas inlet pressure barely changes, so the gas piping is sized correctly. I clock the gas meter at low fire and high fire and calculate the BTU input to be within 99 % of the furnace rating on each stage. This is based on 1,070 BTUs per cubic foot of gas. If this had been in the next county where that utility supplies gas at 1,025 BTUs per cubic foot, the input would have been about 95 % of the furnace rating and I would have increased the manifold pressure from 3.5" WC to 3.7" WC on high fire, and from 1.7" WC to 1.8" WC on low fire. No gas meter calculation factors have to be applied since the elevation here is about 500 feet, gas delivery pressure through the meter is less than 9" WC, and the meter is temperature compensated. I find the sidewall vent termination, check the vent temperature with the Type K bead thermocouple that came with my clamp meter and record that it is 105 °F. With my combustion analyzer, I find 7.3 % carbon dioxide and 10 PPM (parts per million) carbon monoxide. Both of these values are well within the specifications supplied by the furnace manufacturer.
Back inside, I record a return air temperature of 67 °F and a supply air temperature of 137 °F for a temperature rise of 70 °F. For temperatures within a duct, I prefer to use my Fluke 80PK-24 Air Temperature Probe since it has a rigid wand and I can be certain of its placement within the duct. In order to use the entire arsenal of Type K thermocouples that I have collected over the years with my Fluke 902 HVAC Clamp Meter, I purchased a Fluke 80AK Thermocouple Adapter. This adapter interfaces the standard Type K thermocouple mini-pin connector to the standard dual banana plug inputs found on digital multimeters and clamp meters. This will allow me to use my pipe clamp probes, piercing probes, immersion probes, surface probes and air probes with the Fluke 902.
The next measurements I take are important benchmark tests because a definitive initial value is not specified: flame signal and combustion air blower/inducer pressure differential. Both of these are safety devices and have specified minimum values. Once these minimum values are reached, the furnace will no longer operate. By benchmarking the operating values, service technicians can reference these new installation values and compare them to values read during maintenance checks to see if performance has degraded and if action needs to be taken. Flame signal drop-out values and pressure differential make/break values are provided by the manufacturer, but without knowing the changes that may have occurred since installation, one cannot be sure what action, if any, needs to be taken. So I connect my clamp meter in series with the flame sensor lead, set the meter on microamps and record 0.8 microamps. This is 0.64 microamps above the published drop-out value of 0.16 microamps. With direct vent furnaces such as this one, flame signals generally are not as likely to degrade as with furnaces that get their combustion air from within the structure. It all depends on contaminants that may or may not be in the combustion air supply.
Pressure differential created by the combustion air blower will vary from installation to installation depending on vent diameter and equivalent length. These values need to be benchmarked at the time of installation so service techs on future visits know what is "normal" for this furnace in this house. The manufacturer just provides pressure switch make/break settings. So I "tee" into the pressure switch tubing with my incline manometer and measure pressure differentials of 0.9" WC on low fire and 1.5" WC on high fire. On future visits, service techs will know that low fire pressure differential should be 0.4" WC above the break setting and high fire pressure differential should be 0.65" WC above break setting.
My Fluke 902 is proving to be a good choice for an "everyday" meter on today's job so far. On to the next task…