It is an undeniable fact that frequency inverters provide the most benefits of the many methods of controlling induction electric motors. However, in some cases the use of a frequency inverter can have a negative effect on the motor. One of the causes of damage to electric motors due to the inverter effect, happens when the power cable between these two devices is too long. But why?
The output of the frequency inverter is characterized by a PWM signal (Figure 2). Considering this signal, we will observe pulses of variable width, and each of them is characterized by the time of rising and falling of the slope of the signal.

Figure 1. Measurement on the output of VFD with Fluke MDA.
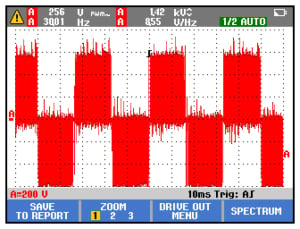
Figure 2. PWM signal on the output of VFD.
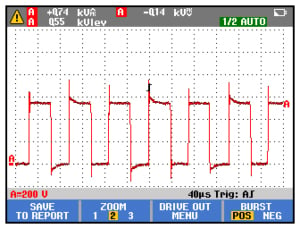
Figure 3. Pulses on PWM signal are characterized by the time of rising and falling of the slopes.
If such a signal encounters the motor terminals while the impedance of the power cord and the motor are not consistent (which is the case when the power cord is too long) the voltage reflectance may occur during this time. In a worst-case scenario, the reflected wave could be added to the fundamental waveform coming from the drive resulting in a significantly higher voltage at the motor terminals.
In the case shown in Figure 5, the peak voltage reached 1.41kV and the rise steepness (dV/dt) was 3.8kV, which was caused by a too long cable between VFD output and motor.
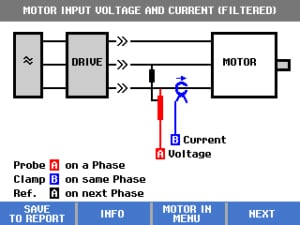
Figure 4. Measurement on the input of the motor with Fluke MDA.
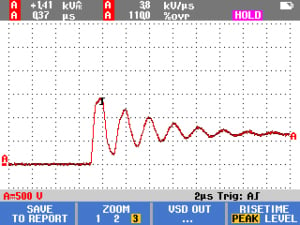
Figure 5. The voltage reflectance phenomenon with the high severity
The voltage reflectance phenomenon can be compared to wave constructive interference.
Both the maximum value of the voltage pulse and the rise steepness (dV/dt) are dangerous for the motor insulation. The insulation of motors with a rated voltage of 400 V is not significantly impaired if the maximum voltage Umax < 1000 V and the steepness of the voltage du/dt < 500 V/μs. In motors designed to operate with VFDs, the permissible values are several dozen percent higher, hence it is worth to specify insulation dedicated for VFDs, when sending an order to the vendor of the electric motors.
How to mitigate effects of the too high voltage rise steepness dV/dt
A tried and tested way to limit the du/dt parameter is to use filter chokes. The task of chokes du/dt is to limit the steepness of voltage rise. This feature increases the life time of the device by protecting the isolation from damage, reducing operating temperature and reducing motor noise. In addition, they allow to increase the motor main cable length from 30 up to 100 meters depending on the switching frequency. These chokes also reduce the propagation of electromagnetic disturbances. At the output of the du/dt choke we should get a perfectly sinusoidal signal. Another aspect is the transmission of noise caused by the frequency switching from the motor to the choke.