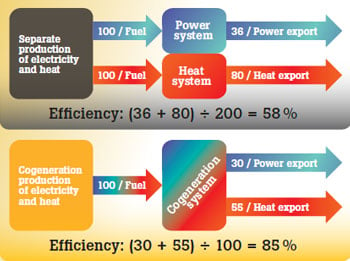
"Cogeneration" captures heat from energy-intensive industrial processes and puts it back to work—to make steam that drives a turbine generator or that heats other parts of the facility, for example. Heat recovery can increase energy efficiency by 30 percent or more. Cogeneration has garnered a lot of attention as a result, and sophisticated, almost turnkey cogeneration solutions are now available in a range of sizes. Even the most sophisticated cogeneration system, however, is an electromechanical system that requires regular maintenance for reliable operation at peak efficiency.
Measurements and maintenance in three key areas of the cogeneration process can help your plant maximize reliability and efficiency:
- Heat recovery
- Mechanical systems and equipment
- Electrical systems
1. Enhancing heat recovery
Anything that allows heat to escape from a heat recovery system reduces efficiency. Insufficient or damaged insulation and failed steam traps are two areas that merit close attention.
Finding bad insulation
To find failed or insufficient insulation, start with a careful visual inspection. A thermal imaging tool is a big help here because what may look good to the naked eye may look completely different when viewed with thermal imager. Inspection of all insulated piping and equipment with a thermal imager should be performed annually and after any maintenance that requires the removal of insulation.
The not-so-humble steam trap
In a typical cogeneration system, heat from exhaust gases is used to preheat water that is fed to a boiler. Steam from the boiler is then piped through the facility for heating or other purposes. Steam traps—devices that remove condensed water from the steam distribution system—are small devices that can have big impacts on the effectiveness and efficiency of a steam delivery system. Steam trap failures are common but can be hard to find. There are two failure modes: open and closed.
A trap that fails closed allows water that has condensed in steam pipes to remain there. Condensed water not only reduces heat transfer and thus efficiency, but water can become entrained in the steam flow, forming a "water hammer" that can damage or destroy equipment as it pounds away like the tool from which it gets its name.
A steam trap that fails open allows steam to vent from the steam distribution system into the condensate return system. A single trap that is stuck open can waste thousands of dollars' worth of steam a year.
To check for proper steam trap operation, you need to be knowledgeable about the steam system you're working on, the type of steam trap you're investigating, and the tools you're using to do the investigation. You often have to be patient and wait for a steam trap to cycle to evaluate its operation correctly.
Three types of inspections can help you to detect failed steam traps:
- Examine the trap for obvious signs of trouble.
Traps that have not been serviced for years may have failure rates as high as 30 percent. - View the trap with a thermal imager.
A thermal imager typically displays objects of different temperature with different colors—often cooler (bluish) colors for cooler temperatures and warmer (reddish) colors for warmer temperatures. A trap that has failed open shows high temperatures on both sides of the trap, because it is venting steam straight through and into the condensate return system. - Inspect the trap with an ultrasonic detector.
An ultrasonic detector works by reducing the high-frequency sounds of steam flow to frequencies audible by the human ear. It also shows sound intensity on a display. This enables a trained technician to use it to detect leaking steam traps.
Set up a steam trap survey program and conduct surveys at intervals determined by the steam system pressure. (See the sidebar, Recommended Maintenance for Peak Efficiency in a Cogeneration Facility.) Technicians can often test several dozen traps per day.
Fortunately, most failures are dirty traps that are either plugged (closed) or leaking (open), and can be repaired easily.
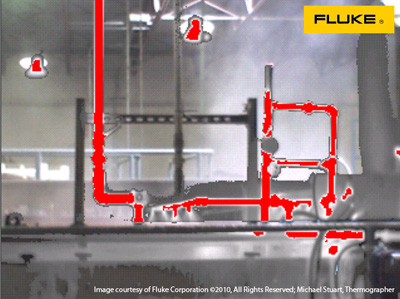
Additional heat leaks to check for
Other leaks that reduce efficiency in the heat recovery system and that can be detected with thermal imagers and ultrasonic detectors include leaking bypass valves, tube leaks, air leaks, and exhaust system leaks.
2. Optimizing mechanical systems and equipment
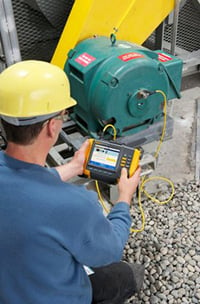
Thermal imaging can also help with troubleshooting mechanical problems that can detract from the efficiency and reliability of a cogeneration operation. A vibration tester can then help find the cause of overheated mechanical parts that have been detected with a thermal imager.
Using thermal imaging to detect mechanical problems
Examine rotating mechanical equipment with a thermal imager to identify abnormally high temperatures. Focus on signs of overheating on motor end bells, which can indicate possible bearing or alignment problems.
Using vibration analysis to detect mechanical problems
The pumps, compressors, and motors that make up a cogeneration system are subject to bearing wear, misalignment, unbalance, looseness, and other mechanical problems. These problems are not only warning signs of premature equipment failure; they contribute to inefficiency as well. Vibration analysis is one of the earliest indicators of mechanical failure. Measuring and analyzing the vibration signature of the machine and identifying abnormalities enable you to access equipment condition during operation. Detecting an incipient bearing failure on the circulating water pump for a heat recovery boiler can prevent unscheduled downtime, and reduced downtime translates to increased plant availability. Excessive vibration can be more than a symptom; it can cause problems itself, causing damage to attached equipment, structures, and seals.
3. Improving electrical systems
Electrical inefficiencies in cogeneration systems can be present in both the electrical generation and distribution system and in electrical equipment that operates as part of the cogeneration system.
If the generator of the cogeneration facility is supplying a large number of inductive loads (for example, motors and transformers), it may be running at a poor power factor. Adding power factor correction capacitors in the electrical distribution system will improve the power factor, and more power from the generator will be available to do useful work in the distribution system.
If the generator is supplying nonlinear loads (for example, VFDs, UPS systems, or copy machines), undesirable harmonic currents may be flowing in the system. These harmonic currents can produce excessive heat in wiring and equipment and cause operational problems with other electronic equipment, including the voltage regulator and controls for the cogeneration unit. Such inefficiencies are often not readily visible, but need to be monitored and controlled.
Survey and log
Conduct a power quality survey of both the cogeneration unit and the electrical system it supplies. This can identify existing and potential problems, including harmonics and distortion of the voltage and current waveforms supplying the cogeneration unit and auxiliary equipment, such as motors and electronic controls.
Use a data logger to record the behavior of the electrical system over time. This is valuable because many power quality problems, such as transients and voltage sags, occur for only a brief period of time. Failure to maintain the electrical system within specified parameters can create excessive heat, cause controls to operate improperly, and reduce the efficiency of electrical production.
The big picture
Reliability and efficiency go together when it comes to operating a cogeneration facility. Individual maintenance issues, such as missing insulation, a leaking mechanical seal, a failed-open steam trap, or an overheating transformer can seem minuscule in comparison to the overall energy production of the cogeneration process, but constant attention to problems can pay big benefits over time.
Look to the heat recovery process and mechanical and electrical systems to find opportunities for improvement. Combining ultrasonic detection, thermal imaging, and vibration analysis is the best use of maintenance technologies available to achieve and maintain a cogeneration plant operating at peak efficiency.
Notes
- Energy Tips—Steam U.S. Department of Energy, http://www1.eere.energy.gov/industry/bestpractices/pdfs/steam1_traps.pdf
- Steam Trap Performance Assessment, U.S. Department of Energy, http://www1.eere.energy.gov/femp/pdfs/FTA_SteamTrap.pdf
- Funding Opportunities, U.S. Department of Energy, http://www1.eere.energy.gov/industry/distributedenergy/funding.html