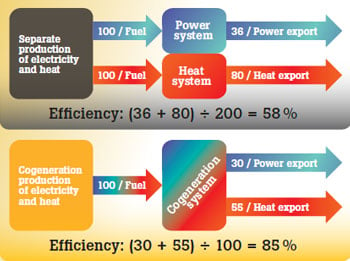
La "cogeneración" captura el calor de los procesos industriales de alto consumo energético y lo vuelve a poner en funcionamiento: para producir vapor que accione un generador de turbina o que caliente otras partes de la instalación, por ejemplo. La recuperación de calor puede incrementar la eficiencia energética en un 30 por ciento o más. La cogeneración ha recibido bastante atención como resultado de ello. Además, las soluciones sofisticadas y aproximadamente de llave en mano de cogeneración están disponibles ahora en todo un rango de tamaños. Incluso el sistema de cogeneración más sofisticado, sin embargo, es un sistema electromecánico que requiere mantenimiento periódico para que haya un funcionamiento confiable a su máxima eficiencia.
Las mediciones y el mantenimiento en tres áreas fundamentales del proceso de cogeneración pueden ayudarlo a maximizar la confiabilidad y eficiencia de su planta:
- Recuperación de calor
- Sistemas y equipos mecánicos
- Sistemas eléctricos
1. Mejora de la recuperación de calor
Cualquier cosa que permita que el calor escape de un sistema de recuperación de calor reducirá la eficiencia. El aislamiento insuficiente o dañado y las trampas de vapor fallidas son dos áreas que ameritan su completa atención.
Localización de un aislamiento dañado
Para localizar un aislamiento fallido o insuficiente, comience por realizar una inspección visual cuidadosa. Una herramienta de termografía es de gran ayuda para esto, puesto que una cámara termográfica puede hacer que se vea completamente diferente lo que se ve bien a simple vista. La inspección de toda la tubería y equipo aislados con una cámara termográfica se debe llevar a cabo anualmente y después de cualquier mantenimiento que requiera desmontar el aislamiento.
La no tan simple trampa de vapor
En un sistema común de cogeneración, el calor proveniente de los gases de escape se usa para precalentar el agua que se conduce hacia una caldera. El vapor de la caldera después se lleva mediante un conducto a través de la instalación para generar calentamiento o para otros propósitos. Las trampas de vapor, dispositivos que eliminan el agua condensada del sistema de distribución de vapor, son dispositivos pequeños que tienen grandes impactos en la efectividad y la eficiencia de un sistema de suministro de vapor. Las fallas en la trampa de vapor son comunes, pero pueden ser difíciles de localizar. Hay dos modos de fallas: abiertas y cerradas.
Una trampa que falla al estar cerrada permite que el agua que se ha condensado en las tuberías de vapor permanezca ahí mismo. El agua condensada no solo reduce la transferencia de calor, sino también la eficiencia, pero el agua puede entrar en el flujo de vapor, lo que formará un "golpe de ariete" que puede dañar o destruir el equipo, ya que golpea con fuerza como la herramienta de la cual recibe su nombre.
Una trampa de vapor que falla al estar abierta permite que el vapor se ventile fuera del sistema de distribución de vapor hacia el sistema de retorno de condensado. Una sola trampa que queda abierta puede desperdiciar cientos de dólares en el valor del vapor por año.
Para comprobar el funcionamiento apropiado de la trampa de vapor, debe conocer el sistema de vapor con el que trabaja, el tipo de trampa de vapor que está investigando y las herramientas que usa para llevar a cabo dicha investigación. Frecuentemente, debe tener paciencia y esperar a que una trampa de vapor realice un ciclo para evaluar su funcionamiento de forma correcta.
Hay tres tipos de inspecciones que pueden ayudarlo a detectar trampas de vapor dañadas:
Examine la trampa y busque señales evidentes de problemas.
Las trampas a las que no se les ha dado mantenimiento por varios años pueden tener tasas de fallos que pueden llegar al 30 %.
Visualice la trampa con una cámara termográfica.
Una cámara termográfica normalmente muestra los objetos con temperaturas diferentes mediante colores diferentes: a menudo colores para temperaturas más frías (azulado) y colores para temperaturas más calientes (rojizo). Una trampa que presentó fallas mientras estaba abierta muestra altas temperaturas en ambos lados, ya que ventila vapor directamente a través y al interior del sistema de retorno de condensado.
Inspeccione la trampa con un detector ultrasónico.
Un detector ultrasónico reduce los sonidos de alta frecuencia del flujo de vapor a frecuencias perceptibles para el oído humano. También muestra la intensidad de sonido en una pantalla. Esto permite que un técnico capacitado use el dispositivo para detectar fugas en las trampas de vapor.
Implemente un programa de análisis en la trampa de vapor y realice dichos análisis a intervalos determinados por la presión del sistema de vapor. (Vea el recuadro: Mantenimiento recomendado para tener eficiencia máxima en una instalación de cogeneración.). Los técnicos pueden a menudo probar varias docenas de trampas por día.
Afortunadamente, la mayoría de las fallas son causadas por trampas sucias que están conectadas (cerradas) o con fugas (abiertas). Además, estas se pueden reparar de forma sencilla.
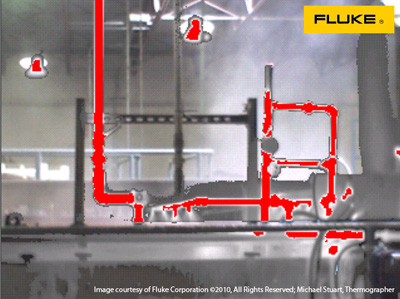
Fugas de calor adicionales que se deben comprobar
Entre otras fugas que reducen la eficiencia en el sistema de recuperación de calor y que pueden detectarse con cámaras termográficas y detectores ultrasónicos se incluyen las fugas en válvulas de desviación, fugas en tubos, fugas de aire y fugas en sistema de escape.
2. Optimización de los sistemas y equipo mecánicos
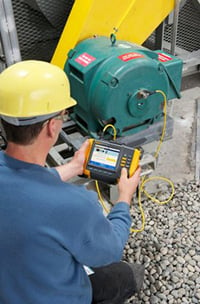
La termografía también puede ayudar con la solución de problemas mecánicos que pueden limitar el valor a la eficiencia y la confiabilidad del funcionamiento de la cogeneración. Un comprobador de vibraciones puede entonces ayudar a encontrar la causa del sobrecalentamiento de las piezas mecánicas que se ha detectado con una cámara termográfica.
Uso de la termografía para detectar problemas mecánicos
Examine el equipo mecánico rotativo con una cámara termográfica para identificar altas temperaturas anormales. Enfóquese en las señales de sobrecalentamiento en las campanas traseras del motor, que pueden indicar posibles problemas en el rodamiento o la alineación.
Uso de análisis de vibración para detectar problemas mecánicos
Las bombas, compresoras y motores que constituyen un sistema de cogeneración están expuestos a desgaste en el rodamiento, desalineación, desequilibrio, soltura y otros problemas mecánicos. Estos problemas no solo son señales de advertencia de falla prematura en el equipo, sino también contribuyen a su ineficiencia. El análisis de vibración es uno de los indicadores tempranos de fallas mecánicas. La medición y el análisis de las marcas de vibración de la máquina y la identificación de anormalidades le permiten acceder a la condición del equipo durante su funcionamiento. La detección de una falla incipiente en el rodamiento de la bomba de circulación de agua en una caldera de recuperación de calor puede prevenir el tiempo de inactividad no programado. Asimismo, el tiempo de inactividad reducido se traduce en disponibilidad incrementada de la planta. La vibración excesiva puede ser más que un síntoma y puede causar problemas en sí misma, lo que generará daños en el equipo, estructuras y sellos anexos.
3. Mejora de sistemas eléctricos
Las ineficiencias eléctricas en los sistemas de cogeneración se pueden presentar en el sistema de generación eléctrica y de distribución y en equipos eléctricos que funcionan como parte de un sistema de cogeneración.
Si el generador de la instalación de cogeneración suministra un alto número de cargas inductivas (por ejemplo, motores y transformadores), es posible que este se encuentre en marcha con un factor de potencia deficiente. La incorporación de capacitores de corrección del factor de potencia en el sistema de distribución eléctrica mejorará el mismo factor de potencia. Así, habrá más potencia disponible desde el generador para realizar trabajo útil en el sistema de distribución.
Si el generador suministra cargas no lineales (por ejemplo, VFD, sistemas UPS o máquinas fotocopiadoras), se podrían estar transmitiendo corrientes armónicas indeseables en el sistema. Dichas corrientes armónicas pueden producir calor excesivo en el cableado y el equipo y pueden producir problemas de funcionamiento en otros equipos electrónicos, incluidos el regulador de tensión y los controles de la unidad de cogeneración. Por lo regular, tales ineficiencias no son fácilmente visibles, pero deben supervisarse y controlarse.
Análisis y registro
Realice un análisis de la calidad de la energía de la unidad de cogeneración y el sistema eléctrico al que alimenta. Esto puede identificar problemas existentes y potenciales, incluidos los armónicos y la distorsión de las formas de onda de la tensión y corriente que alimentan a la unidad de cogeneración y al equipo auxiliar, como motores y controles electrónicos.
Use un registrador de datos para captar el comportamiento del sistema eléctrico a lo largo del tiempo. Esto es valioso, ya que muchos problemas de calidad de energía, como las caídas de tensión y transitorios, se producen solo durante un corto periodo de tiempo. La incapacidad para mantener al sistema eléctrico dentro de los parámetros especificados puede producir un calor excesivo, provocar que los controles no funcionen correctamente y reducir la eficiencia de la producción eléctrica.
La visión general
La confiabilidad y la eficiencia van de la mano cuando se trata del funcionamiento de una instalación de cogeneración. Los problemas de mantenimiento individual, como perder el aislamiento, una fuga en el sello mecánico, una trampa de vapor fallida al estar abierta o un transformador con sobrecalentamiento, pueden parecer insignificantes en comparación con la producción energética total del proceso de cogeneración, pero la atención constante a los problemas que se presenten puede conllevar grandes beneficios con el tiempo.
Observe el proceso de recuperación de calor y los sistemas mecánico y eléctrico para encontrar oportunidades de mejora. La combinación de la detección ultrasónica, la termografía y el análisis de vibración es el mejor uso de las tecnologías de mantenimiento disponibles para alcanzar y mantener una eficiencia máxima en el funcionamiento de una planta de cogeneración.
Notas
- Sugerencias de energía: Vapor Departamento de Energía de EE. UU., http://www1.eere.energy.gov/industry/bestpractices/pdfs/steam1_traps.pdf
- Evaluación del rendimiento de la trampa de vapor, Departamento de Energía de EE. UU., http://www1.eere.energy.gov/femp/pdfs/FTA_SteamTrap.pdf
- Búsqueda de oportunidades, Departamento de Energía de EE. UU., http://www1.eere.energy.gov/industry/distributedenergy/funding.html