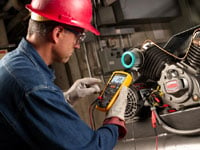
Les variateurs de fréquence (VFD) deviennent de plus en plus populaires. Mis en place sur des ventilateurs et des pompes, ils permettent de réaliser des économies d'énergie et, sur les applications mécaniques, d'effectuer des réglages précis qui ne seraient pas possibles avec d'autres méthodes. Ce ne sont pourtant pas des appareils que l'on branche une fois et que l'on oublie ; ils sont équipés de nombreux composants électriques et sont sujets à toutes sortes de problèmes, des perturbations de l'énergie entrante aux risques environnementaux en passant par les erreurs de manipulations, ainsi que quelques problèmes inattendus. Les moteurs auxquels ils sont assignés posent leurs propres défis.
Dan Orchard travaille dans la maintenance depuis presque 24 ans, il a commencé dans la marine. Il est maintenant technicien senior chez INTIGRAL, Inc., un fabricant de panneaux vitraux en verre isolant scellé, à Walton Hills, dans l'Ohio, aux États-Unis, où il s'occupe de moteurs, de 300 ch à 1/16 ch, et de variateurs de vitesse à longueur de journée. Toutes ces années d'expérience lui ont appris beaucoup concernant l'entretien des moteurs et ce qu'il faut faire lorsqu'un moteur s'arrête. Voici la liste de Dan indiquant ce qu'il faut faire et les erreurs à ne pas commettre.
Commencez par les mesures de base du moteur
Il ne suffit pas de sortir un moteur de sa boîte, le mettre en place et croiser les doigts. Avant de mettre le moteur en fonctionnement, mesurez la résistance des enroulements entre deux phases et mesurez la résistance de l'isolement des enroulements entre la phase et la terre. Orchard utilise un multimètre d'isolation Fluke 1587 pour obtenir les mesures de base.
Mesurez l'intensité de démarrage et de fonctionnement, la tension de fonctionnement et l'équilibre entre les branches.
Mesurez la température lors du premier démarrage, déchargé, chargé et après une période d'utilisation. Un moteur peut chauffer parce qu'il a été beaucoup sollicité, qu'il se situe dans une zone de haute température ou qu'il a un problème. C'est difficile de savoir la véritable raison si on ne connaît pas sa température normale. « C'est bien de savoir s'ils sont en surchauffe ou si c'est normal pour eux, dit Orchard. Bien souvent, on ne remarque pas de problème jusqu'à ce que la chaleur s'accumule, car la température interne normale à proximité des fours de trempe du verre dans mon usine atteint environ 54 °C en été. »

Orchard mesure la température à l'aide d'un thermomètre à infrarouge Fluke 61 ou d'un thermocouple connecté à son 1587 ou à une pince multimètre, et compare souvent les résultats enter les différentes méthodes.
Effectuez d'autres mesures régulièrement
Selon votre planning de maintenance préventive, et le coût des temps d'arrêt non programmés, effectuez des mesures supplémentaires d'intensité, de résistance et de résistance d'isolement. Comparez ces valeurs aux valeurs obtenues précédemment. Si les mesures s'écartent de plus de 5 à 10 %, commencez à rechercher des mauvaises connexions électriques ou des connexions mécaniques desserrées ou inadaptées. Est-ce que la charge a augmenté, la fréquence d'utilisation a-t-elle changé, ou la température ambiante augmenté ou diminué ?
Vérifiez que le moteur correspond à l'application et qu'il soit indiqué pour le système, ou si des mises à jour sont nécessaires.
Vérifiez la protection
Observez les systèmes de protection, les contacteurs de surcharge et les fusibles. La surcharge définie pour l'intensité à pleine charge, est-elle trop haute ou trop basse ?
Les fusibles sont-ils adaptés à l'application ? Les contacteurs de surcharge sont conçus pour protéger des surcharges, alors que les fusibles et les disjoncteurs protègent des courts-circuits. Leurs tailles sont-elles adaptées à la charge ? Le fusible saute-t-il sans déclencher la surcharge ? Les fusibles sont-ils adaptés à l'utilisation ? Si les fusibles sautent régulièrement, on peut être tenté de les remplacer par des fusibles de tension supérieure, mais, par la suite, si la surcharge produit un court-circuit et ne se déclenche pas, ces fusibles, dont la tension est trop élevée, feront griller le moteur. Cela signifie qu'il faudra consulter les antécédents, trouver les manuels (s'ils sont disponibles), ou consulter les données de la plaque signalétique.
Ne vous contentez pas de changer les pièces au lieu de résoudre le problème
Certains techniciens changent des pièces jusqu'à ce que le problème disparaisse. Cette manière de dépanner est très onéreuse, puisque la plupart des moteurs et variateurs coûtent au minimum 500 $. Il arrive qu'un moteur/variateur tombé en panne fonctionne à nouveau dans une autre application.
Il en devient donc plus difficile de cerner le problème d'origine, puisque la panne n'était que temporaire. Est-ce la charge, l'application ou une combinaison de facteurs qui est responsable de la panne ?
Les câbles également peuvent poser problème
Vérifiez la ligne au niveau du moteur, pas seulement au niveau du panneau mural, qui peut être situé à une trentaine de mètres. Les lignes électriques dans des milieux hostiles (par exemple, à des températures élevées), peuvent tomber en panne même si elles sont protégées par des conduits. Vérifier la tension au panneau et non au moteur peut entraîner le remplacement d'un moteur en parfait état alors que le problème peut se situer dans le câblage.
Consultez la configuration et les paramètres du variateur. Vérifiez les temps d'accélération et de décélération. Utilisez-vous la fréquence secteur, une fréquence supérieure ou inférieure ?
Assurez-vous de choisir le bon moteur
Parfois les moteurs sont utilisés pour des applications tout autres que celles auxquelles ils sont destinés. Les moteurs à ondulateur font toute la différence dans la durée de vie du système. Par exemple, utiliser un moteur standard de 50 Hz aboutit souvent à une surchauffe. De même, le faire fonctionner à 90 ou 120 Hz peut réussir pendant un certain temps, mais le moteur ne pourra pas supporter cette fréquence de manière continue.
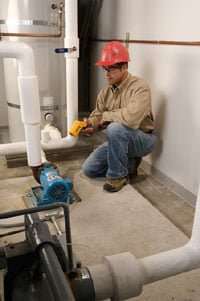
Le cycle de service des moteurs permet de déterminer l'application pour laquelle ils sont adaptés. Un moteur conçu pour fonctionner 8 heures par jour, 5 jours par semaine tombera en panne prématurément s'il doit fonctionner 24 heures sur 24, 7 jours sur 7.
Les données indiquées sur la plaque signalétique sont importantes pour un dépannage. Elles indiquent le facteur de service du moteur, son cycle de service, etc. Elles fournissent également des données essentielles concernant les circuits de protection et les fusibles.
Vérifiez les problèmes d'alimentation
De nombreuses défaillances de variateur sont causées par des pics d'énergie, des pertes de phase ou des sous-tensions. Après un problème d'alimentation, il est important de mesurer le courant pour savoir si le problème est corrigé ou s'il est encore en cours. Si vous ne vérifiez pas l'alimentation après une coupure de courant, les variateurs en feront les frais. Lorsque le courant revient après une coupure, il se peut que les opérateurs de la machine la redémarrent et tentent de la remettre en fonctionnement automatiquement. « Soudain les variateurs sautent et les moteurs grillent à cause du fonctionnement monophasé, car de nombreuses machines essayent de démarrer », dit Orchard.
La plupart des variateurs récents sont configurés pour ne pas laisser le système redémarrer après une défaillance. Orchard configure le sien pour que rien ne soit négligé, même pas une section manquante de 480 V AC, avec des indicateurs de perte de phase pour aider l'équipe de maintenance à identifier les problèmes.
En résumé
Dan pourrait en parler pendant des heures. Vous pouvez le trouver sur le forum Test Tool Talk sur Fluke Nation