If your small team doesn’t include a Master Electrician and maintenance specialists, consider investing in these five electrical troubleshooting tools to quickly identify basic electrical issues in HVAC, networks, motors, and electrical panels. After a few tests with these tools, you’ll know if a specialist needs to be called in or not, saving your team time and money.
As with all electrical work, opening panels and measuring electricity can be dangerous. Be sure to take the time to wear appropriate personal protective equipment (PPE) and follow all safety regulations, like lockout/tagout standards or your region’s guidelines.
1. Troubleshooting HVAC using an infrared thermometer
An infrared thermometer, like the Fluke 64 MAX, can help troubleshoot malfunctioning HVAC mechanical systems. Using a thermometer to check for issues can help you catch them before you start hearing unusual sounds from your HVAC system, increased dust from the unit, additional energy bill costs, or an odd smell. Use the thermometer to check and regularly recheck for:
- Electric heating coil operation
- Steam trap temperatures
- HVAC panel power supplies
- Boiler hot water temperature
- Thermostat accuracy
- Refrigerant coil surface temperatures
- Condenser temperatures
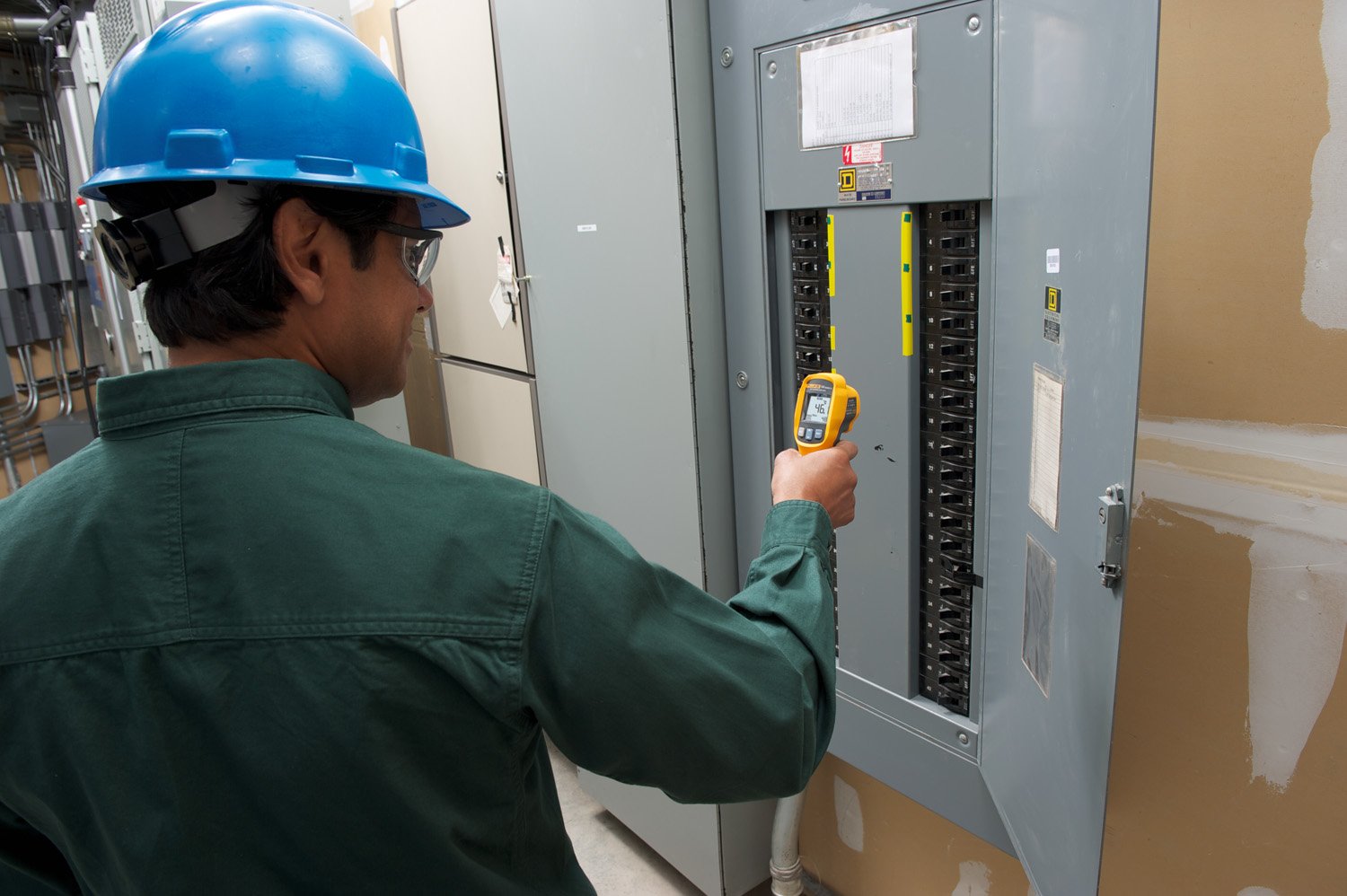
And, since the thermometer allows for temperature measurements from further away, you can also use the tool to safely check for hot and cold spots, the discharge air temperature, air distribution in ducts, and temperature of ceiling-mounted equipment.
Work the point-and-shoot thermometer into your operation maintenance plan and create a baseline for normal temperatures on HVAC equipment and on motors and panels throughout your facility. As you check through the facility, make note of any temperature measurements that are higher or lower than your baseline. When you discover discrepancies, you’ll know it’s time to call in a maintenance specialist and where you need them to look.
2. Troubleshooting panels and motors with a thermal camera
A thermal camera can be a powerful preventive maintenance tool for identifying basic issues, such as overheating in panels and motors. If too much heat is created in a panel or motor, a thermal camera can spot it without opening covers. Keeping up with regular thermal scans and inspections throughout your facility can ensure you detect problems early on so you can have them repaired before they cause large failures.
The Fluke PTi120 pocket thermal imager is small enough to carry around all the time. Similar to the IR thermometer, you’ll want to use the thermal camera to scan assets for a baseline and look for temperature changes after that. Using the asset tagging feature on the PTi120 can help your team track assets and inspection images.
Though small enough to keep in your pocket or bottom of the tool bag, the PTi120 is also powerful enough to pinpoint possible issues with a wide temperature range of -20°C to 150°C. The images show up on a 3.5” screen offering IR-Fusion overlay. It’s both simple and fast to check your equipment.
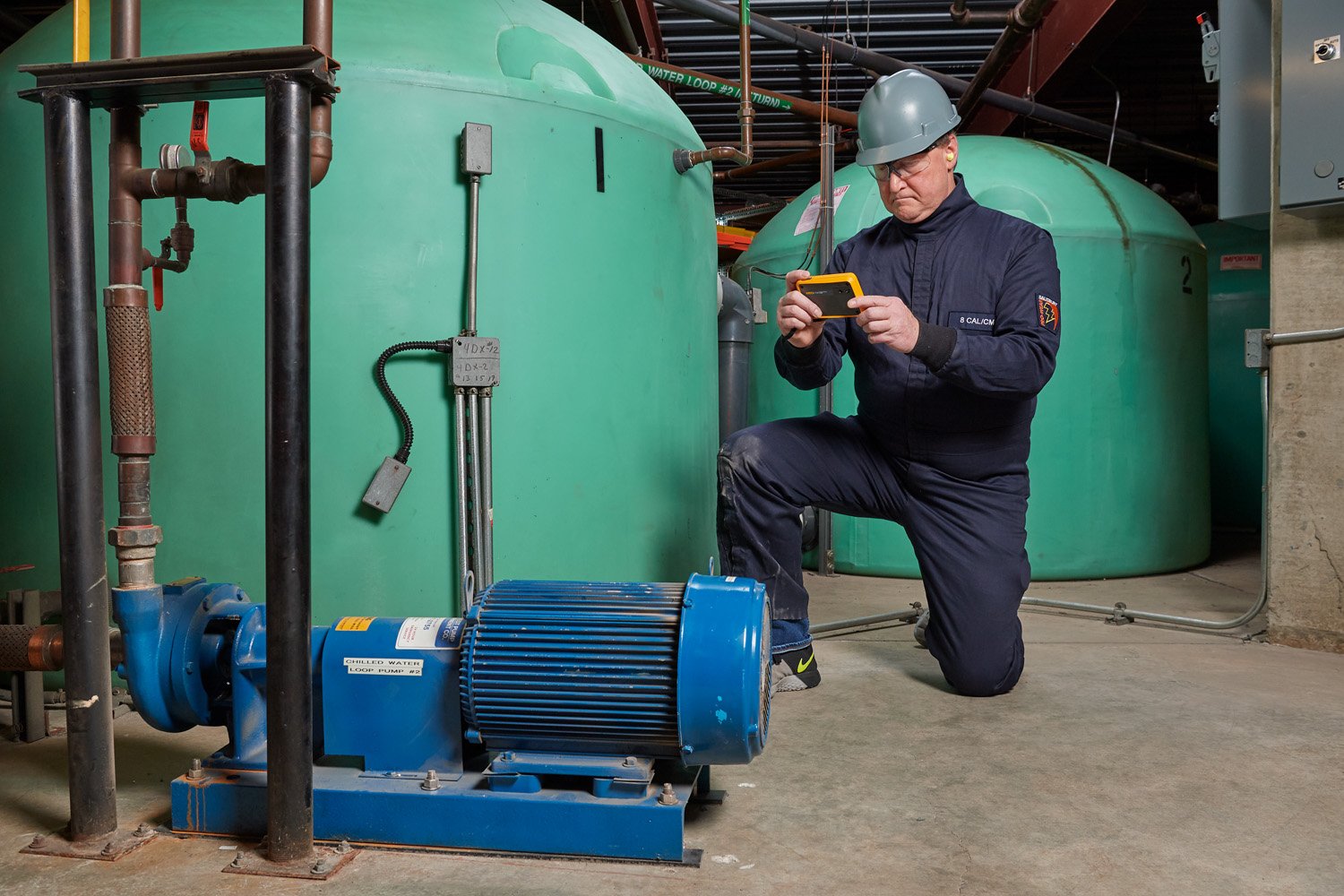
3. Troubleshoot panels with an electrical tester
An electrical tester can help you recognize possible issues in electrical panels. If power isn’t getting to an asset, starting at the panel with an electrical tester can help you determine where along the line that issues is whether it’s a defective breaker or a problem with incoming power.
Including a Fluke T6-1000 Electrical Tester in your tool bag will make for quick and easy AC current and AC voltage and frequency measurements. With FieldSense™ technology, measurements can be made through the open fork, the widest available in the industry, without needing to contact a live wire. While you still need to take the safety regulations into account and dawn the proper PPE to make these measurements, it’s a lot faster when you don’t need to pull out test leads.
Verify absence of voltage or see all the power supply measurements with one quick glance. If you notice the measurements are off from the asset manufacturer’s specs, you likely have a problem. This gives you the information you need to justify a maintenance team looking and knowing what kind of issue they’re looking for.
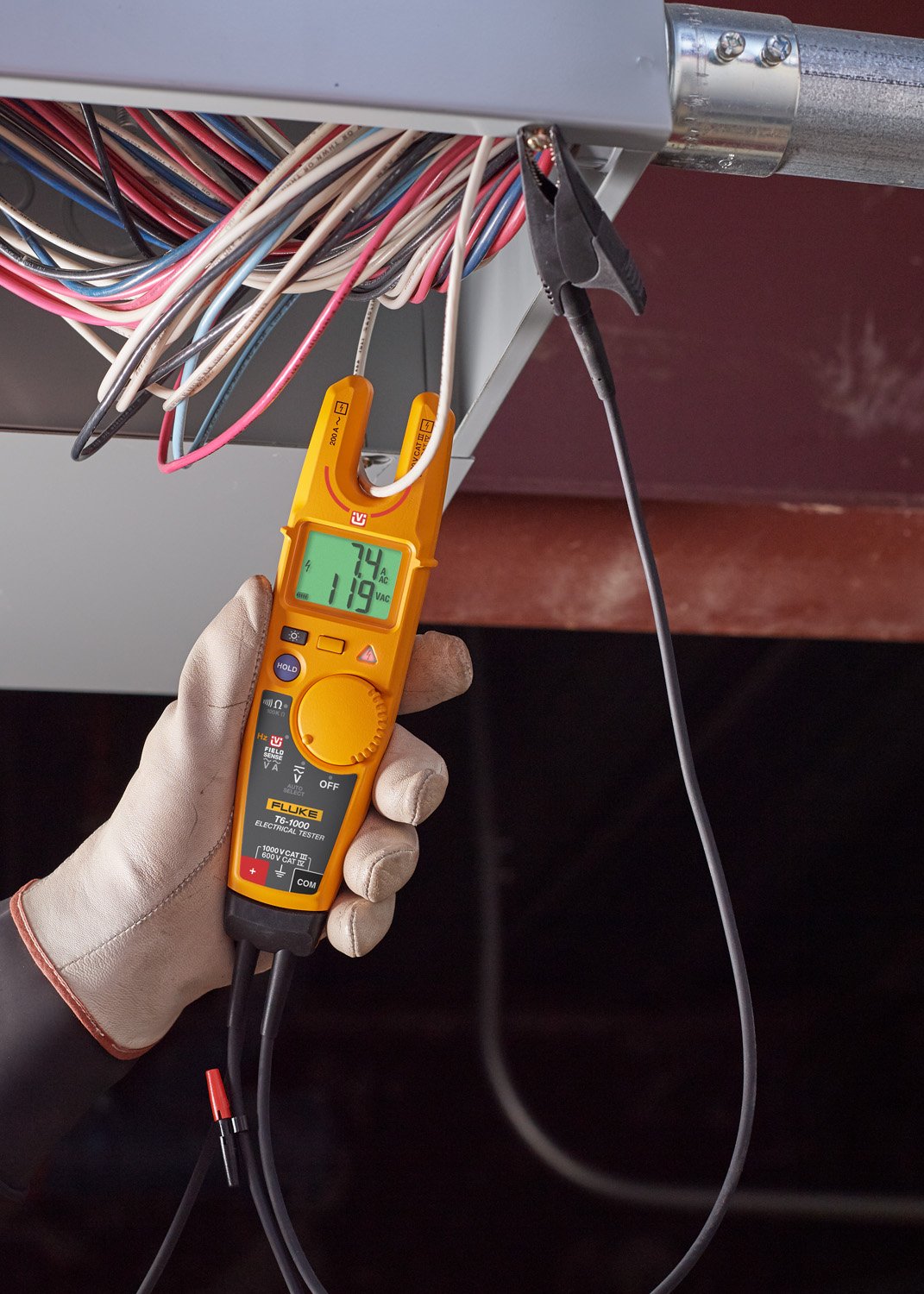
4. Troubleshoot and monitor rotating machinery with vibration sensors
Including a vibration sensor in your preventive maintenance tools and equipment is an easy step to monitor the assets in your facility and quickly realize issues with motors and drives. All motors and drives vibrate and over time, these vibrations can cause expensive issues, for example, shaft imbalance or looseness, misalignment, or bearing wear. These kinds of issues often cause a cascade effect leading to further damage down the line if not caught and repaired quickly.
The Fluke 3561 FC Vibration Sensors can be installed in about an hour and scaled just as easily to cover an entire building, especially when paired with Fluke Connect™ Condition Monitoring (FCCM) software. These sensors track triaxial vibration screening and temperature trends on your equipment. The sensors will be able to track changes over time so you can know if something on your motors is wearing down. The data can give you an idea of when to schedule maintenance because temperature can be the first indication of impending failure in motors, pumps, and bearings.
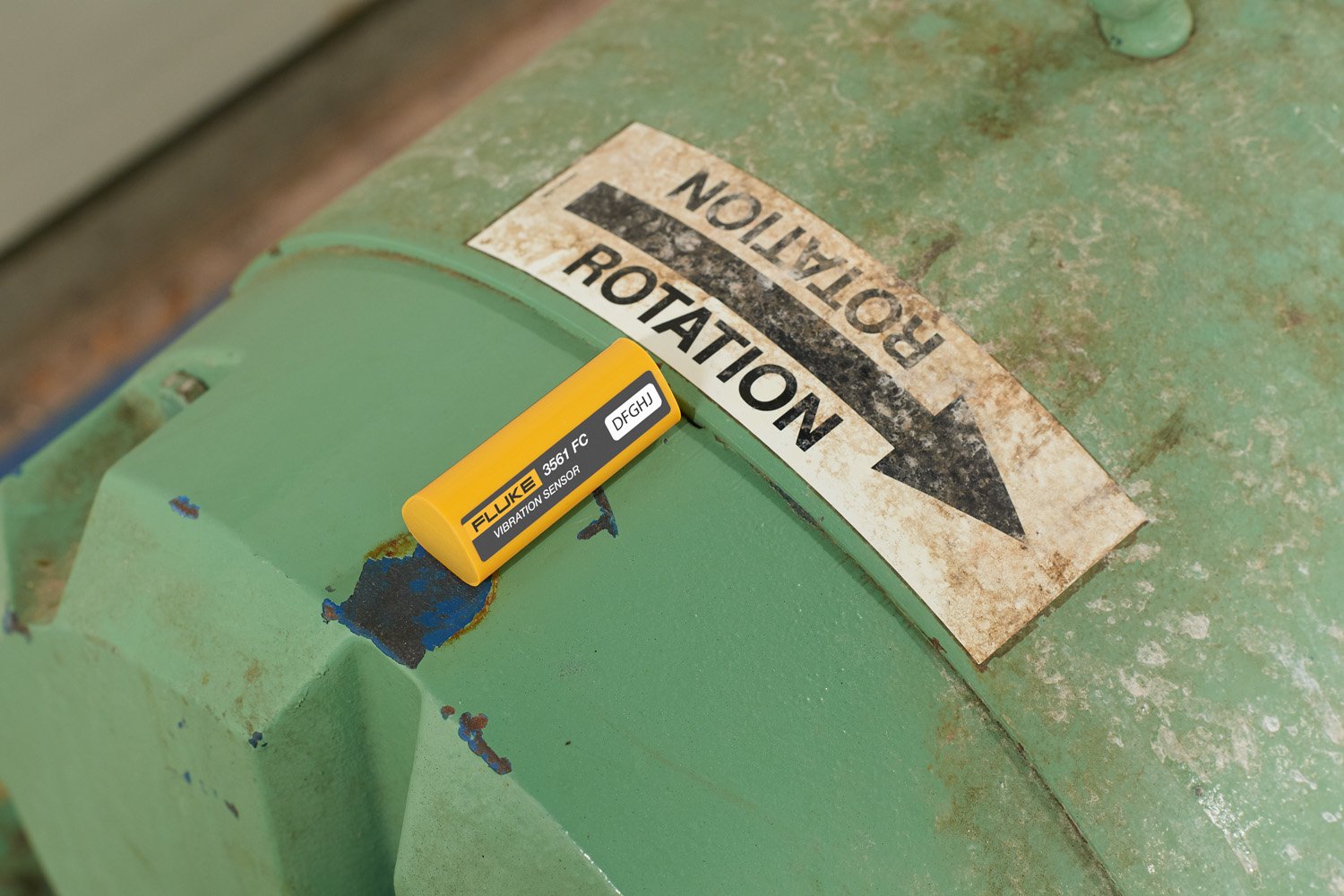
5. Troubleshoot network issues with a fault locator
If you have an issue with your network, the faster you can locate it, the faster you can have it fixed. A malfunctioning cable may cause intermittent network connections, or your facility may experience no connection at all.
Adding a Fluke Networks’ VisiFault™ Visual Fault Locator (VFL) to your facility maintenance equipment list will help you diagnose simple fiber link problems so you don’t need to call in the specialists every time. The VisiFault™ is a cable continuity tester your staff can implement without much training. The laser-powered tester can help find breaks in cables, connectors, and splices. It can also locate fibers and verify cable continuity and polarity, which you can see easily with both continuous and flashing modes. Designed to work with both 2.5mm and 1.25mm connectors for easy connection and hours of battery life mean your team can easily implement this maintenance tool.
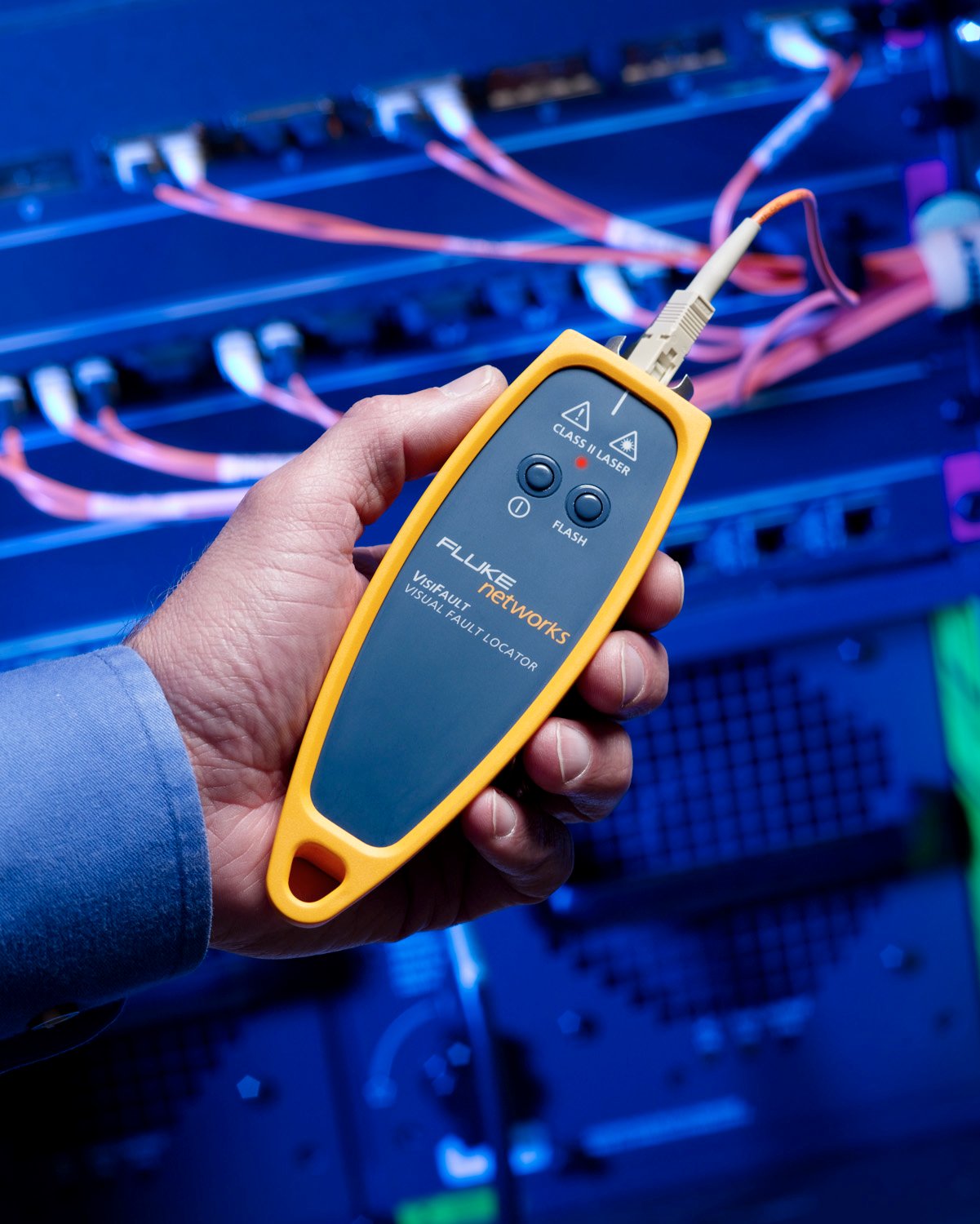