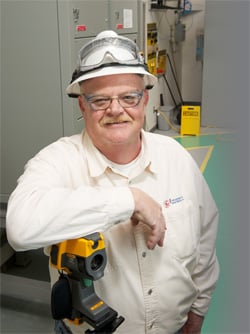
The uninterruptible power supply (UPS) system provides backup power for critical plant loads in every industry. Those loads include plant emergency and safety shutdown systems, plant alarms and controls, emergency lighting, generators, steam and fire control systems, telephone centers, and even hospital life support systems, among others. Needless to say, the UPS system can't fail…period.
Jerry Rainwater, Power Consultant for Industrial Power and Battery, Inc., deals with that challenge on a daily basis. "Our company's mission is to ensure the continuity of critical power to make sure businesses stay in business," says Rainwater. Rainwater got his start in the US Navy nuclear submarine program as a system expert working on the Trident missile system and subsystems. "I knew I had found my calling," Rainwater recalls. "Working with electricity is a rewarding job as long as you never forget 'safety first.'"
He has been installing, servicing, and troubleshooting many different types of UPS and battery systems for more than 30 years. He started in 1980 aboard his first submarine, the USS Benjamin Franklin. After he left the Navy, Rainwater worked for Westinghouse Engineering Services in Dallas, Texas. Then, in 1989, he was recruited by Solidstate Controls, Inc. to start a UPS Service Center in Houston, Texas.
After meeting that challenge, Jerry has been with Industrial Power and Battery—based in Wallisville, Texas—since 2003. The company services UPS systems in refineries, petrochemical plants, telephone centers, power plants, and hospitals throughout Texas.
Keeping the UPS up
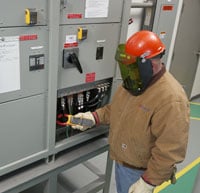
A UPS system includes a battery, a battery charger, an inverter, a static switch, and a manual bypass switch. This system converts the stored energy of the battery into ac power. "The inverter keeps the plant systems running so that if there is an abrupt interruption in power, plant staff can continue to monitor all of their safety equipment and other systems and control the process of bringing the systems down safely with no environmental—and hopefully no human—impact," says Rainwater. This is especially crucial for petrochemical plants where interrupting the refining process could have explosive results.
A typical preventive maintenance call finds Rainwater first checking all of the electrical systems for hot spots or loose connections. He has been using mostly Fluke test tools since his time in the Navy. "Fluke really is the standard, whether you're working on a nuclear sub or in a petrochemical plant," says Rainwater.
He usually starts by surveying the power cables going into the UPS system with his Fluke Ti25 thermal imager to make sure that there aren't any hotspots, and that none of the readings are trending higher than reported during the previous maintenance inspection. Next he moves to the electrical distribution panels to survey the status of the plant electrical environment. If he finds problems, he makes a verbal note using the audio recording capabilities on the camera so he can review it later with the client.
Once the overall environment is squared away, Rainwater focuses on the UPS system. "I start by taking 'as is' readings on the battery charger with my Fluke 189 True RMS DMM," he says. "Then I take individual cell voltage readings, measure the voltage drop across each cable or bus bar connection, and measure ac ripple voltage and frequency, and cell temperature and hydrometer readings, on each battery," says Rainwater. "With these measurements, you can determine the overall health of the battery."
Choosing highly rated safety tools and test equipment
With the types of environments he works in, safety is paramount. "When you're installing a new UPS system or replacing a battery, the battery is always energized so you have to use electrically rated hand tools and proper Personal Protective Equipment based on the hazards you may be exposed to," says Rainwater. Safety is even more important for his test equipment. It helps that the Fluke 189 has a CAT III 1000 V/CAT IV 600 V safety rating. And when he needs to enter an area that requires intrinsically safe equipment, he can take his Fluke 87V Ex Industrial Multimeter.
After testing the charger and the batteries, Rainwater uses a 100 MHz ScopeMeter® 105B Series II portable oscilloscope to check inputs and outputs and highs and lows for the circuit boards that control the battery charger, the inverter, and the static switch. "All those UPS components have their own controls, and all have to talk to each other to make sure they're all working right," says Rainwater. He also uses his ScopeMeter test tool to record the static switch transfer from the normal inverter power source to the bypass power source. "A mechanical switch is too slow, so we use a static switch consisting of a group of fast-operating silicone controlled rectifiers (SCRs) to switch the critical loads," Rainwater says. "The SCRs must transfer from normal to bypass power in less than 4 milliseconds so the computers stay energized and the lights don't blink. Fortunately, my ScopeMeter can accurately measure the static switch at that speed."
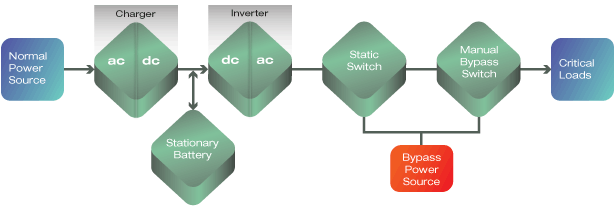
He estimates that his job is about 90 percentage scheduled maintenance and 10 percentage emergency response. In addition to installing and maintaining UPS systems, Rainwater also maintains generators, generator controls, automatic transfer switches, emergency lighting systems, ac and dc distribution panels, fire pump controllers, and motor control centers, and analyzes power quality.
Sizing systems to the job
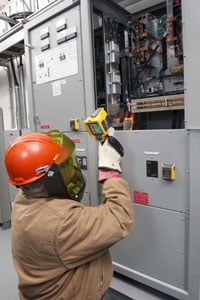
Industrial Power and Battery is helping one of its long-time customers, Zeon Chemicals LP, more than double the size of its UPS system in its Bayport, Texas plant. Zeon Chemicals is the leading developer and supplier of innovative polymers, including synthetic elastomers that are used in the manufacture of hoses, seals, gaskets, belts, and other parts for automotive, industrial, oil field, and printing markets. In addition to the Bayport plant, Zeon has plants in Hattiesburg, Mississippi and Louisville, Kentucky, where it is headquartered.
Industrial Power and Battery will replace Zeon's 7.5 KVA UPS system with a new 20 KVA UPS system later in 2012. The increased size was based on a load analysis of current use and projections for added demand resulting from Zeon's expansion plans. They plan to expand production, increasing capacity by 25 percentage in 2012.
The 22-year-old Zeon Bayport facility includes a maintenance shop, laboratory, and administration building, in addition to the 20,000-square-foot plant. Approximately 50 people work at that location, including Debbie Miller, an Instrument Electrical Technician responsible for repairing and maintaining plant instrumentation and automation equipment. She has worked at the Bayport location for as long as it has been open, and has worked with Jerry Rainwater for the last 10 years.
Miller shares Rainwater's affinity for Fluke tools and uses them almost exclusively for predictive and preventative maintenance tasks. She surveys all of the electrical equipment in her area with the Fluke Ti25 thermal imager calibrates instruments with the Fluke 1587 Insulation Multimeter. "I find Fluke meters to be accurate, durable, and designed with features a technician appreciates," says Miller.
Because Miller has her hands full with maintenance and troubleshooting, she's glad to have the services of Industrial Power and Battery to take care of the UPS system. "We depend on the UPS system to back up our emergency lighting, fire alarm system, telephones, plant security equipment, and, of course, the DCS controls," says Miller. "Since we're a small company and the UPS system is a critical system for us, it's nice to work with a full service company like Industrial Power and Battery that has the knowledge and expertise to maintain and service it for us."