Highly successful manufacturing plants rank high in availability, performance, and quality. A plant’s most substantial capital investments are in their facilities and equipment, and most manufacturing systems are built to meet a specific capacity level that meets demand. This is why capacity maintenance is critical to the success, and competitiveness, of manufacturing plants today.
The more efficiently a company can produce a product, the more products it can produce at a lower cost which results in higher profit margins.
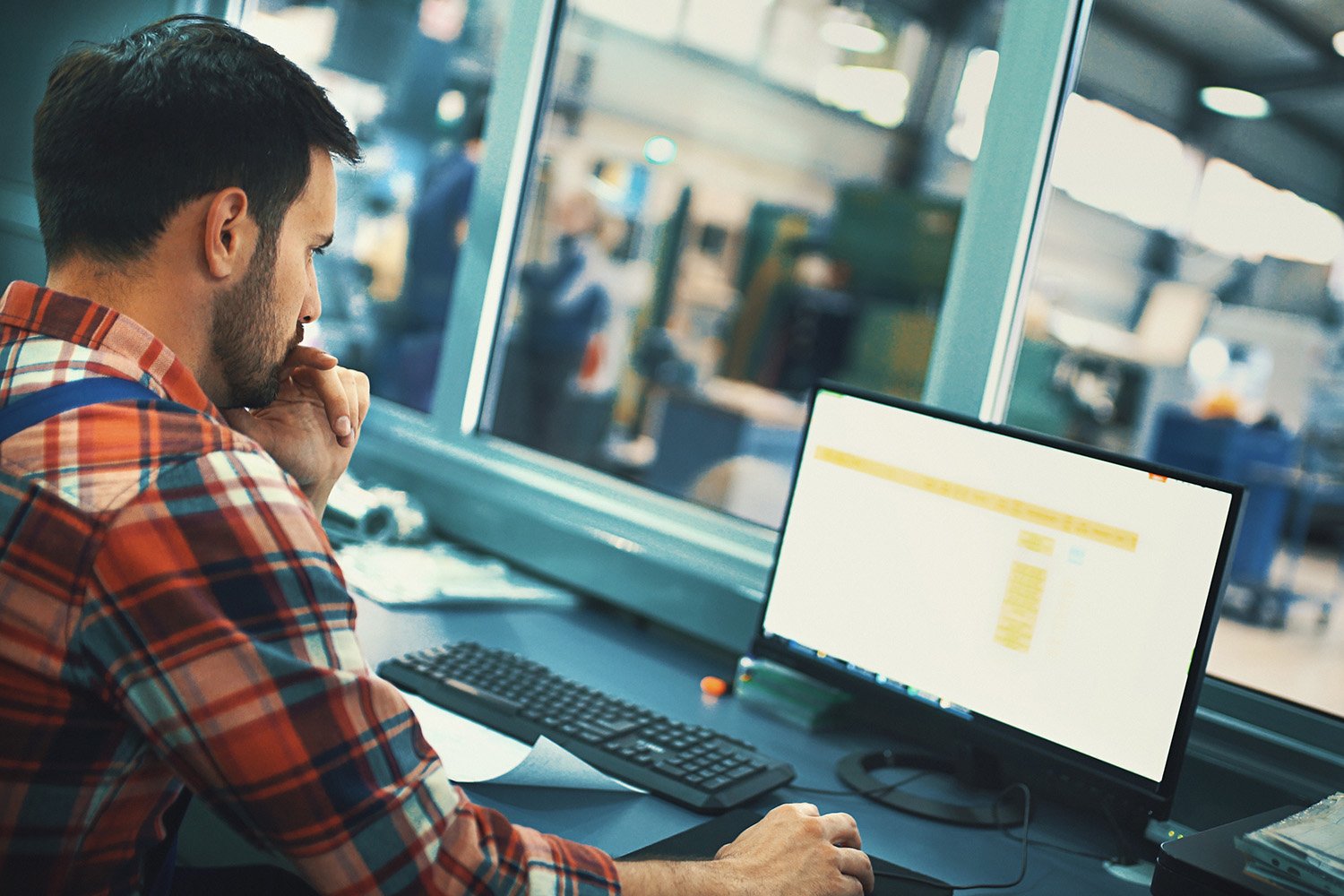
A key performance indicator (KPI) for manufacturers is their OEE score—Overall Equipment Effectiveness. The OEE score is based on these three factors:
- Availability: operating real time (ORT) to planned time (PT)
- Calculation: ORT ⁄ PT
- Areas of Loss: Unplanned stops and planned stops
- Performance: real speed (RS) to planned speed (PS)
- Calculation: RS ⁄ PS
- Areas of Loss: Small stops and reduced speed
- Quality: valid pieces (VP) to total pieces (TP) produced
- Calculation: VP ⁄ TP
- Areas of Loss: Production rejects and startup rejects
The OEE score is calculated by multiplying plant availability, performance, and quality.
Availability (%) X Performance (%) X Quality (%) = OEE (%)
A plant with an OEE score of 100% would reflect 100% planned uptime, 100% planned speed, and 100% of pieces produced being accepted for quality. A perfect OEE score is not only unreasonable to expect, it is also unattainable. At some point in time, every plant schedules downtime for planned maintenance or changeovers. A good OEE score is considered 85%.
Improving the OEE Score
Start with a baseline OEE score by capturing plant data over a month.
- Availability: How many hours was the plant up and running? How many hours was it expected to be available? Calculate the score by dividing the expected number of hours into the actual number of hours.
- Performance: How many products were processed by the machines and equipment? How many products were expected to be processed? Calculate the score by dividing the expected number of products into the actual number of products.
- Quality: How many products were produced? How many products were accepted for quality? Calculate the score by dividing the number of products produced by the number of products that were accepted.
Here is an example score card for a manufacturer that runs continuously for 30 days and was designed to manufacture 50 products per hour:
Availability | Expected hours of up time | 720 | Actual hours of up time | 688 | 95.55% |
Performance | Expected number processed | 36,000 | Actual number processed | 30,960 | 86.00% |
Quality | Number produced | 30,960 | Number accepted | 26,935 | 86.99% |
The OEE score for this manufacturer would be calculated as:
Availability (95.55%) X Performance (86.00%) X Quality (86.99%) = OEE (71.48%)
This is the breakdown for the three OEE categories:
- Availability: This manufacturer was down 32 hours in the month for planned maintenance and changeouts.
- Performance: During the hours of uptime, the manufacturer produced 45 items per hour.
- Quality: Approximately 13% of products produced are rejected.
To achieve a good OEE score of 85%, each of the individual categories needs to reach a minimum score of about 95%. In the example, the losses are shown in the performance and quality categories. For this manufacturer to maximize system capacity, they need to improve performance by about 9% and quality by about 8%.
Also, consider that when performance is improved, the number of products manufactured will increase and potentially impact the quality score.
Start with a Strategy
Regardless of the product manufactured, all manufacturing plants have the same issue. Over time and with use, machines and equipment experience diminished or degraded output. The “O” in OEE refers to Overall—which means no machine or piece of equipment left behind. All machines and equipment must be maintained to ensure reliable availability, performance, and quality.
There are, however, two essential groups of machines and equipment that should be top of mind for every plant manager, and both are critical to the success of the plant.
- Revenue Critical: There is a direct relationship between each percentage of incremental performance and the incremental revenue of the company. These assets directly determine the company’s ability to win, and by how much. They need constant assessment, regardless of condition, and must always run at peak performance.
- Production Critical: These assets must be up and running for the company to make money. Performance is less of an issue than whether the asset is on or off. If things are spinning, conveyors are moving, or hydraulics are actuating, the company can generate revenue. Uptime is the KPI, and the ability to anticipate pending failures is highly valuable.
These assets don’t need to be big, expensive, complex, or heavy duty. Sometimes a chemical process can depend on a simple solenoid valve, or a food processing line can depend on whether a $20 motor is dispensing material out of a hopper.
Criticality is not about how complex a piece of equipment is, but rather about the effect it has on the plant’s ability to generate revenue.
Key Performance Parameters
It is no secret that when machines are maintained to a high standard, they hold their tolerances better, reduce scrap and rework, and improve part consistency and quality. Since most manufacturing plants are built to meet demand, they have little-to-no access to additional capacity. This means that every piece of equipment in the plant must perform as expected for as long as possible to maintain plant uptime and deliver consistent quality.
When considering the revenue critical machines and equipment, it is necessary to understand their Key Performance Parameters (KPP). The KPPs are measurable values the equipment needs to maintain throughout its workable lifetime. It is not enough to ensure “up and running” for these revenue critical assets when a manufacturer wants to compete at a high level.
For example, here are the KPPs for an air operated, two ball, double acting pump.
Air Inlet Pressure Range | 600 – 2070 PSI (47.6 – 142.8 bar) |
Maximum Rec’d Cycles/Minute | 70 |
Displacement In3 Per Cycle | 59.8 |
Volume/Cycle | 33.1 oz (979.6 ml) |
Cyclers Per Gallon | 3.9 |
Flow @ 70 Cycles/Minute | 18.1 GPM (68.6 LPM) |
Noise Level @ 60 PSI – 40 CPM | 89.8 db(A) |
Why is this information important? Because these parameters are the guide to performance success for that piece of equipment. Maintaining equipment to their KPPs extends their life, reduces unplanned downtime, and ensures production quality is consistent.
Gathering this type of data for every piece of revenue critical equipment in a plant may be a daunting task, but it is necessary to complete before a maintenance planning approach can be developed. Note that this is a one-time audit—from that point forward it is modified as new equipment is added and other equipment is retired.
Having the KPP data for critical equipment is what gives one maintenance team the competitive edge over another.
Maintenance and Reliability Planning
The four most common maintenance approaches used in manufacturing plants today include after-the-fact (reactive), preventive, predictive, and automated/self-maintaining. Knowing a good reliability strategy would include a mix of reactive, preventive and predictive, the latter two are the most active maintenance approaches a manufacturing plant will use to ensure maximum equipment availability, performance, and quality.
Preventive maintenance is usually manually applied using test and measurement tools that gather real-time data and information about a piece of equipment. Predictive maintenance includes condition monitoring, data collection, and the use of a computerized maintenance management system.
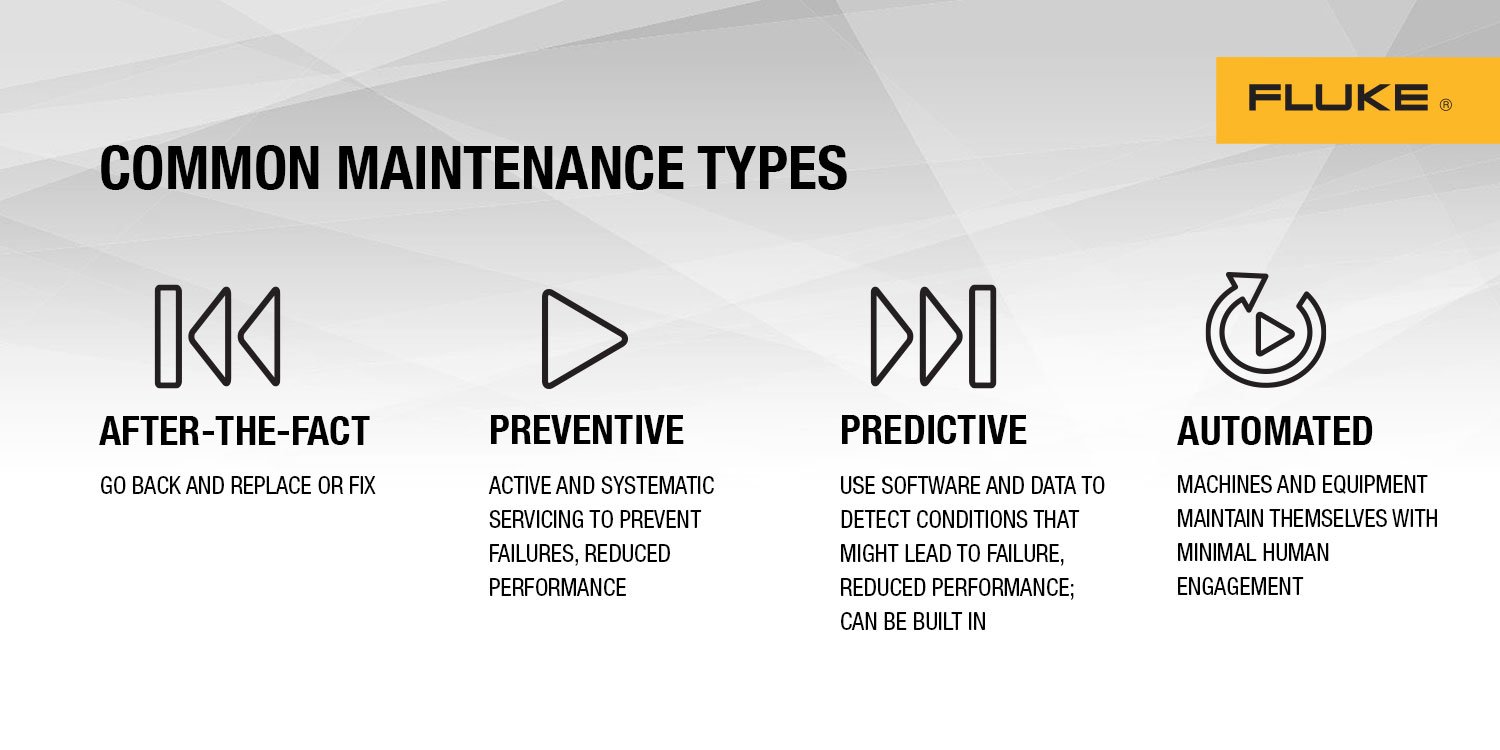
Bringing all the right elements, tools, and resources together to build a strong and effective maintenance program takes planning and strategy. Below are examples for how to approach each of the different OEE categories, the tactics that can be implemented into a maintenance program, and some recommended tools for each tactic.
Availability
Objective: Ensure uptime by eliminating unplanned equipment failure and minimizing planned stops.
Approach: Use a combination of wireless data collection and hands-on maintenance to ensure maximum uptime for each piece of equipment.
Tactic 1: Add computerized maintenance management system (CMMS) software to eliminate data gaps and silos and enable the maintenance team to make data-driven decisions about asset health and maintenance priorities. eMaint is an asset reliability platform that helps manufacturers increase uptime by integrating a select combination of maintenance and condition monitoring tools and software solutions.
Tactic 2: Establish a regular maintenance schedule for each machine to reduce failures and extend equipment life. Preventive maintenance intervals are typically based on equipment manufacturer recommendations. A good clamp meter and insulation multimeter will go far to meet most preventive maintenance test and measurement needs.
Performance
Objective: Maximize equipment speed by eliminating small stops and issues that reduce speed.
Approach: Ensure the power sources for equipment are maximized. This includes power quality and compressed air systems, as well as motors and battery systems.
Tactic 1: Add power quality monitoring and power quality studies. Taking power quality measurements helps identify the sources of poor power quality and energy waste and helps protect equipment from future damage. Most power quality issues occur within the manufacturing facility, but it is important to test power quality at the service panel as well.
Tactic 2: Address compressed air and gas leaks. An estimated 30 to 50% of a compressed air system’s capacity is lost to leaks. That impacts the performance of all equipment that uses compressed air or gas. Use a sonic industrial imager to detect, size, and quantify the costs of compressed air/gas system leaks.
Tactic 3: Identify hot spots that could cause equipment failures or reduced capacity. Use an infrared camera, or thermal imager, to capture baseline, trending, and comparative thermography data. Thermal imaging inspections provide immediate visual temperature measurements that can be used to make decisions about the health and performance of a piece of equipment.
Tactic 4: Test individual stationary batteries and battery banks to ensure measurement threshold and tolerance ranges are maximized. Use a battery analyzer that allows for predefined thresholds to be added for quick PASS, FAIL, WARN notifications.
Tactic 5: Ensure automation industrial communications are not disrupted by Electromagnetic Interference (EMI) or other environmental factors that corrupt vital information between devices (e.g., sensors, logic blocks, variable frequency drives) and programmable logic controllers and distributed control systems, and cause machines to stop. Use network traffic tools to identify high loss network nodes and a CableAnalyzer™ to find network cables susceptible to disruption.
Quality
Objective: Ensure maximum number of valid pieces manufactured by reducing production rejects and startup rejects.
Approach: Use vibration and alignment testing along with calibration to ensure precision and accuracy in equipment and machinery.
Tactic 1: Test equipment for excessive vibration and bearing condition. Vibration includes acceleration, velocity, and displacement units of measurement.
Tactic 2: Perform precision shaft alignments on rotating machinery to prevent early bearing and seal failures along with excess energy waste.
Tactic 3: Calibrate equipment back to factory standard to eliminate excess wear and early deterioration.
Achieving manufacturing excellence
To become a highly successful manufacturing plant, availability, performance, and quality must be top priorities. With the right data, resources, and tools, a well-designed maintenance plan can move a manufacturer from average to top competitor. The maintenance culture must be focused on improvement, best practices, and continuous learning—without these, there can be no success.
Remember…
- The more efficiently a company can produce a product, the more products it can produce at a lower cost which results in higher profit margins.
- Criticality is not about how complex a piece of equipment is, but rather about the effect it has on the plant’s ability to generate revenue.
- Having the KPP data for critical equipment is what gives one maintenance team the competitive edge over another.